TM 1-1500-204-23-2
4-19. Dampening and Absorbing Units. Dampening and
absorbing units retard the motion of moving objects to
which they are attached.
These units perform this
function by removing some of the energy of motion and
converting It to heat. The heat is then dissipated into the
atmosphere. Dampening and absorbing units used in Army
aircraft are hydraulic dampers, shock struts, and liquid
springs.
a.
Hydraulic Dampers. A damper is a device for
controlling the speed of relative movement between two
connected objects Usually, one end of the damper is
connected to a fixed member; the other end, to a movable
part. The reacting parts of the damper move against
considerable resistance. This resistance slows the speed of
relative movement between the objects. Hydraulic dampers
used in Army aircraft operate either by displacing fluid or by
shearing fluid.
(1)
Displacement-principle
dampers.
Displacement-principle dampers used in Army aircraft are of
two types-piston and vane.
Though
different
in
construction, both types have the same basic design
characteristics-a sturdy metal container with a sizeable
Inner space divided into two or more chambers. The
chambers vary In size according to the position of parts
within the damper. The chambers must be completely filled
with fluid in order to operate properly.
(a) Piston damper. A typical piston damper is
shown in figure 4-162. Note in figure 4-163 that the piston
and rod assembly divides the space within the damper
housing into two chambers Seal rings on the piston prevent
fluid leakage between the chambers. An orifice permits
fluid to pass with restricted flow from one chamber to the
other. A filler port (not shown) provides for servicing the
damper with fluid.
1.
Operation. As the piston is forced to the
right, chamber 2 decreases in proportion to the distance the
piston IS moved. Simultaneously, chamber 1 increases by
a comparable size. The hydraulic fluid displaced from
chamber 2 flows through the restricting orifice into chamber
1. When the piston is moved toward the left, reverse
changes occur in the chamber sizes and in the direction of
fluid flow. The restriction of the fluid flow by the orifice
shows the rate of speed at which a given amount of force
can move the damper piston. The rate at which a damper
moves in response to a force is called damping rate or
timing rate. In some dampers, the opening is of fixed size
and timing rate is not adjustable. In other dampers, the
orifice size is adjustable to allow for timing adjustments.
2.
Nose landing gear damper. The nose
landing gear of an aircraft has a tendency to shimmy when
the aircraft is taxiing at any appreciable speed. A damper
is used as shown in figure 4-164 to eliminate wheel
shimmy without interfering with the normal steering
movements on the nose wheel.
3.
Rotor blade damper. Piston-type dampers
are used on helicopter rotor head assemblies and on tail
rotor hub assemblies to control lead-lag movements of
rotor blades. Note in figure 4-165 how the dampers are
connected Lead-lag movements of rotor blades occur In
cases In which there are three or more blades in a set and
the blades are hinged to the rotor head.
(b) Vane damper. A typical vane-type damper is
shown in figure 4-166. This type of damper consists
basically of a cylindrical housing having a polished bore
with two stationary vanes (called abutments) and having a
shaft supporting two movable vanes. Together the four
vanes split the cylinder bore lengthwise Into four
chambers as shown in figure 4-167. The two stationary
vanes are attached to the damper housing The two
movable vanes, along with the shaft, make up a unit
called a wing shaft. The wing shaft rotates between the
abutments. One end of the wing shaft is splined and
protrudes through the damper housing. A lever arm,
attached to the splined end, is the means of rotating the
wing shaft.
1.
Operation. The damper chambers are
completely filled with fluid, and at any Instant of damper
motion the fluid is subjected to forced flow. As the wing
shaft rotates, fluid flow between the chambers takes place
through an opening within the wing shaft, which
interconnects the four chambers. Thus a restraining force
is developed in the damper, dependent on the velocity of
fluid flow through the orifice. Slow relative movement
between the wing shaft and the damper housing causes a
low velocity flow through the opening and little resistance
to damper arm rotation. More rapid motion of the wing
shaft Increases the speed of fluid flow and thus increases
resistance to damper arm rotation. The timing rate of
vane-type dampers can be adjusted by a timing
adjustment centrally located in the exposed end of the
wing shaft. This adjustment (not shown) sets the effective
size of the opening through which fluid flows between
chambers and thus determines the speed of movement
with which the damper will respond to an applied force.
4-157
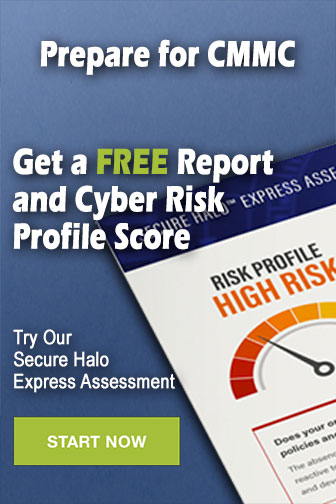