TM 1-1500-204-23-6
CHAPTER 2
HARDWARE
2-1.General. This technical manual provides general information, and is intended to be used as a guide rather than for
specific applications. The technical manuals for each type aircraft provide specific instructions for the use and
application of hardware and consumable materials. There is no document published that provides data on substitution of
hardware. Substitution of hardware is only authorized by engineering changes for improvement and effectiveness of
efficient application and operation of a given segment of equipment. There is no general interchangeability of items
listed in Air Force Navy Aeronautical Standards (AN), Military Standards (MS), and National Aerospace Standards (NAS),
since each item listed is engineered to a specific standard. The trend is to gradually replace the AN standards with the
MS standards as the MS standards are accepted by all segments of the Armed Forces. When the change occurs, the AN
standards become obsolete and are deleted from the military supply system. NAS has been established to provide
hardware for specific applications requiring exacting tolerances, finishes, and strengths. These items are applied to
military aircraft where engineering decisions dictate their use in lieu of AN and MS hardware. Replacement of NAS items
is made in those areas where engineering and design activities decide that the same function can be performed by the
replacing part without sacrificing quality on a specific item of equipment.
2-2.Bolts. Most aircraft structural bolts are either general purpose hexagon head bolts, internal wrenching bolts, or close
tolerance bolts. Aircraft manufacturers are sometimes compelled to make bolts of different dimensions or higher
strength than the standard types. Since these bolts are made for a particular application, it is extremely important that
like bolts be used for replacement. When such bolts are not available, and it is necessary to fabricate them locally, care
should be taken to use identical material and heat treatment specified in the applicable drawings or an authorized
substitute material properly heat-treated. These special bolts are identified by the letter S stamped on the head.
a.
Grip Length. As a general rule, bolt grip lengths should be kept equal to material thickness. The threads should
neither bear on the material, nor should the shank protrude. Certain variations are allowed as this is not always possible.
Bolts of slightly greater grip length than that required may be used provided washers are placed under nut or bolt head.
Where plate nuts are used, add shims under the plate. Aluminum alloy washers should be used, except in cases of high
torque values, with steel bolts in duralumin parts for prevention of corrosion. Steel washers should be used with steel
bolts on steel parts.
NOTE
Steel bolts and aluminum alloy washers should be installed while still wet with, MIL- P-
23377 epoxy polyamide primer.
b.
Installation and End Description. Whenever possible, bolts should be installed with the bolt head up, outboard or
forward to prevent the bolt from falling out, should the nut come loose. On rotating controls, heads should be installed in
the direction of rotation, except where interference occurs. The shape of the bolt ends varies as shown in figure 2-1.
Bolts A and B show varied chamfer angles, bolt C shows a flat end, and bolt D a round or pointed end.
c.
Locking or Safetying. All bolts should be suitably locked or safetied in accordance with the method used in
original fabrication of the aircraft. Approved methods of safetying are specified in paragraph 2-17
d
Bolt Head Identification. Bolts are designed and fabricated of different materials and with different tensile
strengths for their individual heat ranges and grip stresses. Each bolt is marked with a code for identification and
physical characteristics. See table 2-1 for these code markings.
2-1
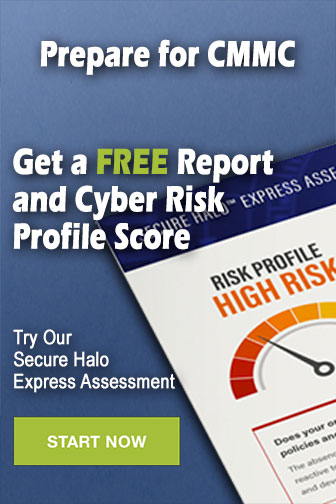