TM 1-1500-204-23-2
of the actuating cylinder is placed in the off position, fluid is trapped in the chambers on both sides of the actuating
cylinder piston. This locks it against movement in either direction.
(3)
Allowable leakage. The seepage of some fluid past shaft end seals and bearings is necessary
for their lubrication. However, through normal wear, seepage develops into leakage. Moderate leakage at piston rod end
bearings and seals during operation is normal in actuating cylinders which have been in use for some time. There are
established limits as to the amount of leakage permitted at such points. The general military specification for allowable
external leakage at each shaft seal and bearing is one drop per 25 cycles of operation (25 full or partial strokes in each
direction). This specification is applicable except where a different leakage limitation is specifically stated in publications
for the equipment concerned.
(4)
Maintenance. Care of hydraulic actuating cylinders shall be as specified in applicable aircraft
maintenance manual. Typical troubleshooting data is outlined in table 4-40.
(a)
To reduce excessive wear and possible failure of hydraulic cylinder packing rings,
exposed part of piston rod shall be cleaned as follows:
1
Remove foreign materials by wiping with a clean cloth saturated with hydraulic
fluid, MIL-H-5606 or MIL-H-83282.
2
If extreme foreign materials are encountered, clean before and after each flight.
3
If operating in freezing temperature, cleaning is accomplished easier
immediately after landing.
(b)
Replace hydraulic cylinders when the rod becomes scratched, nicked, or dented deep
enough to cause leakage.
(c)
When overhauling hydraulic cylinders, all ferrous metal parts will be magnetic particle-
inspected for cracks and flaws. Inspection will be accomplished in accordance with TM 55-1500-335-23, and TM
551500-204-23-7 Parts will be marked properly after inspection.
Figure 4-133. Single-Action Actuating Cylinder
4-134
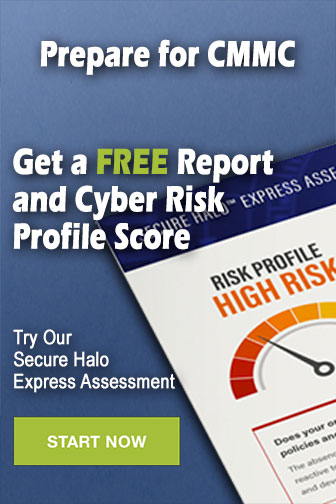