TM 1-1500-204-23-2
Table 4-40. Troubleshooting Actuators
Trouble
Probable Cause
Remedy
Leakage from operating end
Packing around piston rod is
Disassemble cylinder and replace
of piston
leaking
packing, if worn
External leakage around head
Lockring holding gasket is
Tighten
and base
not right
Gasket is worn
Replace with new gasket
Leakage from one side of
Packing on piston is worn or
Disassemble and replace
piston to the other
scored
packing
Packing Inside piston is worn
Disassemble and replace
or scored
packing
Piston is not securely fastened
Tighten nut holding piston on
to piston rod
piston rod
Smooth finish on barrel is
Overhaul
scratched or scored
h.
Ratchet Valve. Hydraulic ratchet valves are used as companion devices to double-action actuating
cylinders. The purpose of a ratchet valve is to aid an actuating cylinder in holding a load in the position into which it has
been moved by operation of a hand pump. The ratchet valve insures that there will be trapped fluid on each side of the
actuating cylinder piston. This is necessary for the actuating cylinder to lock a load against movement in either direction,
and is especially vital should the selector valve which controls the actuating cylinder be left in the on piston or have
Internal leakage. The ratchet valve does not affect actuating cylinder piston movements that are intentionally produced
by means of system operating pressure. Ratchet valves are optional equipment and are used only in cases where
locking a load in position is of great importance. In figure 4-136, the ratchet valve is shown with no pressure applied
(selector valve off ). The piston is centered in its bore, and both check valves (balls A and B) are closed. This locks the
actuating cylinder in position by trapping all fluid in the cylinder. The ratchet valve is shown in figure 4-137 with pressure
applied to port 1. This forces the piston to the rig ht where it unseats ball check B. Pressure entering port 1 unseats ball
check A on the left side. Fluid then flows through the ratchet valve, and the piston moves to the right, unseating ball
check B.
i.
Hydraulic Servos. Many situations exist in which powered movements must be consistently made with
accuracy within thousandths of an inch; such exact control cannot be effected by an actuating cylinder merely connected
with a selector valve. Hydraulic servos perform this function. Hydraulic servos are used in both airplanes and
helicopters to multiply the physical effort expended by personnel in operating the aircraft. Servos enable a pilot to use
fingertip force in controlling the actions of a flight control system that may actually require hundreds of pounds of force to
actuate.
(1)
Design. In effect, a hydraulic servo is a combination of an actuating cylinder and a selector
valve in a single unit. The servo selector valve is manually opened by the operator and is automatically closed by the
servo's movement. The spool-shaped valving device of the servo selector valve is commonly referred to as a pilot
valve. Servos are made in two general designs. In one design, the servo cylinder housing is stationary and the piston
rod moves. In the other design, the piston rod is stationary and the cylinder housing moves. For convenience, a servo in
which the
4-136
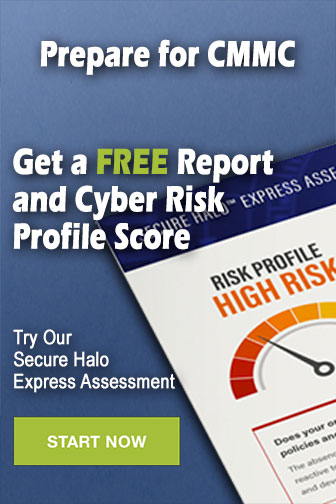