TM 1-1500-204-23-2
and size of the aircraft on which the brakes are installed. These discs are keyed to the wheel and rotate with the wheel.
The brake piston housing, which is securely bolted to the torque plate of the aircraft landing gear, contains from one to
four brake actuating pistons, the number depending on the type and size of the aircraft. Depressing a brake pedal forces
hydraulic fluid through connecting lines to the wheel brake assembly and Into each piston cavity. This forces the piston
and the outboard brake lining against the brake disc. Since the disc is free to move from side to side along the lugs in
the wheel, it is forced against the inboard brake lining. The friction that results from this clamping of the rotating disc
between a pair of linings retards the continued rotation to the disc and of the wheel to which it is attached.
(a)
Single-disc. Figure 4-155 shows a cross-section of a single-disc brake. This brake, like
most hydraulically operated disc brakes, is self-adjusting. The illustration shows a cutaway of only one piston cavity.
However, all piston assemblies of this type of brake are nearly identical.
1
Application. Application of the single-disc brake occurs when hydraulic fluid
under pressure enters the fluid port (7). This pressure forces the piston (5) to the left against spring pressure until the
spring guide (6) contacts the flanged side of the adjusting pin (8). In moving this distance, the piston has forced the
outboard brake lining (4) against the steel disc (3), which in turn moves sideways on its keys and contacts the inboard
brake lining (2)
Figure 4-154. Disc Brake Assembly
supported by the backing plate (1). The brake running clearance is thus taken up by this first movement of the piston.
However, to obtain full braking friction between the rotating disc and the lining "pucks", the piston must move farther to
the left. The disc must be firmly pinched between the lining "pucks". The spring guide is already contacting the face of
the adjusting pin, and the adjusting pin is held firmly by the friction of the adjusting pin grip (9). However, pressure on
the piston provides enough force to overcome this faction, allowing the piston and pin to move farther to the left If the
brakes are held in this applied position, the lining wears away. The pin continues to move Inward slowly to compensate
for the small amount of lining wear.
2
Release. Each time the brakes are released, the piston backs away from the
outboard lining block. It can move until the back of the piston head contacts the face of the adjusting pin. The piston
always releases to give the same running clearance. The self-adjusting pin grip prevents the pin from moving to the
right.
(b)
Dual-disc. Dual-disc brakes, which are always multiple piston types, are used on aircraft
requiring more braking faction at lower pressure than single disc brakes provide. Pressure applied to the pistons of this
type of brake pushes their attached linings against the brake disc nearest the pistons. That disc is then forced against
the brake linings on its side of the center carrier assembly. This forces the center carrier assembly and its second set of
brake linings against the second disc. The second disc is then forced against the brake linings in the anvil. In this
manner, each brake disc receives equal braking action on both sides when the brake is operated. When brake pressure
is released, the return springs within the self-adjusting mechanism in each cavity retract the pistons.
(2)
Parking brake valves. Parking brake valves are used on some aircraft wheel brake systems as a
means of trapping fluid pressure in the wheel brake assemblies to keep the brakes applied for parking. Individual and
dual type valves are commonly used. Because the dual type is basically a combination of two individual valves, this
explanation of the dual valve will illustrate the operation of both types.
(a)
Operation. The typical dual parking brake valve shown in figure 4-156 Incorporates two
spring-loaded pistons in compensator cylinders, which provide an automatic means of compensating for changes in
hydraulic oil volume caused by temperature
4-149
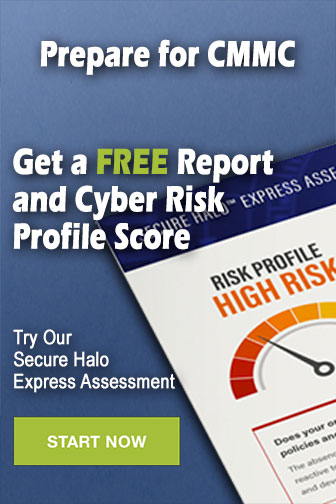