TM 1-1500-204-23-2
(a) Internal inspection. The various con-
structions of hose assemblies are inspected as follows:
1 Straight hose assemblies. Insert light
at one end and inspect by looking through from the
opposite end.
2 Hose assembly with elbow fitting one
end. Insert flexible inspection light into elbow fitting
and examine by looking through from the opposite end
3 Hose assembly with elbow fittings both
ends. Insert flexible inspection light into one end and
examine from the opposite end using a dental-type
mirror. This procedure is practical on large size hose
assemblies only.
(b) Other configurations and small size hose
assemblies. Pass a ball of proper size (refer to table
4-13) through the hose assembly to check for restriction
or kinking.
d. Instructions for Repair of Flexible Rubber Hose.
Replace all defective hose assemblies without attempt-
ing repair. MS28759, MS28762, MS28741, and AN
6270 hose assemblies are field fabricated, and are
replaced as a complete unit. However, fittings from the
old hose assemblies should be reused on the new
assemblies when they are in good condition All factory
assembled hose, or field assembled hose which has
been in storage, shall be subjected to pressure test prior
to installation in accordance with paragraph 4-5f
e. Instructions for Assembly of High Pressure
(3000 psi) Hose Assemblies MS28759 and MS28762.
High pressure hose assemblies MS28759 and
MS28762 are fabricated from high pressure bulk hose
conforming to MIL-H-8788 or MIL-H-8790, and fittings
conforming to Military Standards MS28760 and
MS28761
(1) Visually check bulk hose. Visually check
bulk hose when hose Is cut for assembly. Check hose
for mutilations, mandrel joints, marks, seams, and ex-
cessive graphite
(2) Visually check fittings. Check fittings for
Mutilations, nicks, and distortions caused
be overtightening, scratches, or other
damage to the cone seat sealing surface.
Backed out retaining wires on swivel nuts.
Mutilation or other damage to threaded areas.
Damage to the finish which would affect
the corrosion-resistance of the fitting.
NOTE
Do not intermix the socket and nipple from
one manufacturer with those of another. All
fittings are marked with the manufacturer's
symbol Also, do not reuse aluminum sock-
ets on high pressure hose fittings.
(3) Equipment required. The following equip-
ment is required for field fabrication of high pressure
hose assemblies:
Wire brush or soft wire wheel.
6 inch slip-joint pliers.
Knife (leather or linoleum), ground as
shown in figure 4-39.
Fine tooth hacksaw.
10,000 psi hydrostatic test machine.
Standard wrenches.
Shop vise.
(4) Determine correct length of hose. Deter-
mine correct length of hose required as shown in table
4-14 and figure 4-40. Cut hose squarely using a fine
tooth hacksaw. Using compressed air, clean hose after
cutting to remove all cutting residue.
(5) Hose and fittings assembly. Assemble
hose and fittings using following procedures and figure
4-41, steps 1 through 9:
4-38
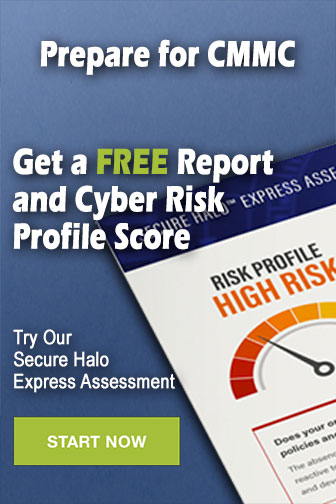