TM 1-1500-204-23-2
4
Recheck position angle to be sure position angle has not changed.
(b)
Method for special elbow bends and/or preformed hose. Special elbows and preformed hose are
positioned as follows.
1
Assemble one end of the hose assembly as described above.
2
Determine required angles. Required angles may be obtained from the hose assembly part
number by comparison with a known good hose assembly or with an assembly mocked-up on the installation. Preferably
the assembly to be repaired should be set up on a fiat surface, vises and parallels set and clamped, and required angles
set on protractor before the assembly is disassembled See figure 4-48, details I, J, and K for this setup.
3
Establish base positions and check angle, drop dimension and assembly length. Angle
vises shall be tilted so that the flange mounting plates are parallel to the face of the flange and the flange mounting holes
lined up with the bolt holes already tapped in the mounting plates. Any necessary spacing with parallel bars shall be
done at this time. When this procedure is followed properly, the result will be a fixture with the proper angles, drop
dimensions, and lengths established. See figure 4-48, details I, J. K, and L for this setup.
4
Complete fitting assembly by mounting in vise to hold elbow or hose from turning while
tightening to required gap.
5
Recheck position angle to be sure position angle has not changed.
(12)
Proof test procedures. Proof test all hose assemblies after assembly for a minimum period of 30
seconds and maximum period of 5 minutes, using Tester, Hose Assembly, Part Number 78344, FSN 4920-00-855-9035.
(a)
Proof test pressures. Recommended proof test pressures are listed in table 4-23.
NOTE
Proof pressures for flange fittings are reduced to avoid possible distortion of the flange and shoulder by
exceeding design pressure limitations for flange fittings.
(b)
Proof test medium. Proof test medium shall be hydraulic oil, MIL-H-5606.
(c)
Cleaning. Clean and drain hose assembly after proof test as directed in paragraph 4-5i (9).
NOTE
Application of an identifying mark such as a paint dot, indicating satisfactory proof test, is recommended.
(d)
Capping. Cap or plug all hose assemblies to ensure cleanliness.
(13)
Installation. The following procedures and precautions will be followed when installing Teflon hose
assemblies (see figure 4-49).
CAUTION
Do not place wrench on socket of hose fitting when installing hose assembly. Failure to comply will
compromise the strength and integrity of the union between the hose and fitting.
(a)
Route and securely clamp. Teflon hose assemblies to avoid abrasion, and particularly to prevent
kinking where flexing occurs.
(b)
Eliminate chafing against structure, moving parts, or other assemblies by clamping and use of
chafing guard if necessary.
(c)
Support Teflon hose assemblies by clamping every 24 inches. Closer support is preferred if
possible. Support flexible hose assemblies by clamping so that they cannot cause deflection of rigid connecting
assemblies. Support clamps shall not restrict travel or cause hose to be subjected to tension, torsion, compression or
shear stress during flexing cycles. Select proper size support clamps as indicated in table 4-24.
4-65
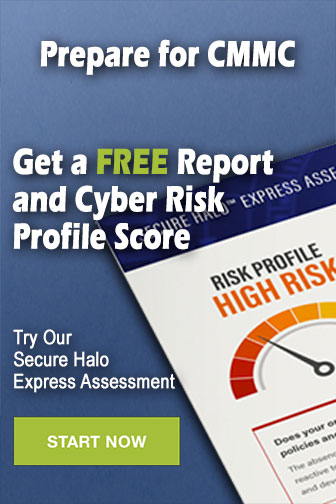