TM 1-1500-204-23-2
To eliminate the possibility of hose failure by
mismatch of similar type fittings, all MS and
NAS numbers shall be verified by supervisory
and/or quality control personnel to ensure
that the MS or NAS number is correct for that
particular application.
(c)
Hose assemblies identification. The fol-
lowing paragraph describe how to identify factory fabri-
cated, locally manufactured or tested Teflon hose as-
semblies.
1. Factory fabricated. Factory fabri-
cated Teflon hose assemblies are identified by a perma-
nently attached metal band marked with the appropriate
specification, operation pressure in psi, assembly part
number, date of proof test, and hose manufacturers
code number
2. Locally manufactured or tested. Lo-
cally manufactured or tested Teflon hose assemblies
shall be identified by a metal band made from Federal
Specification QQ-A-250/8C, 5052-0 aluminum alloy,
0.020 inch thick, 0.75 inch wide, in accordance with fig-
ure 4-42. The markings on the band may be impression
stamped, etched or engraved to include date of pressure
test, Federal Stock Number of part number, operating
pressure, and depot or unit code or name. If the pressure
test date is more than one year prior to installation in the
aircraft or system, the assembly shall be retested and
banded prior to installation. Original manufacture date of
all retested hoses shall be brought forward on to the new
band, if available.
(3) Handling and inspection. Refer to paragraph
(4) Disassembly. Refer to paragraph 4-5i (7).
4-5i (3), (4).
(5) Cleaning. Refer to paragraph 4-5i (9).
Hose assembliesconforming to MIL-H-25579
and hose assemblies conforming to
MIL-H-38360 use different hose and fittings.
DO NOT interchange components between
assemblies. Improper combinations of hose
and fittings lead to life endangering failures.
Used end fittings and aircraft hose shall not be
reused in fabrication of MIL-H-38360, Aircraft
Hose. Failure to comply will compromise the
integrity of assembled hoses.
(b) Assembly procedure for high pressure
Teflon hose (MIL-H-36360). See figure 4-50. The follow-
ing steps shall be followed when fabricating hose assem-
blies from new components.
1. Hose length. Determine hose cutoff
length by subtracting fitting cutoff factor from the hose
assembly length or by calculating the length from the
information shown on the hose assembly drawing (see
table 4-27). The cutoff length may also by determined by
measuring the used length of hose being replaced. Cut
hose squarely. A hose cutoff wheel is recommended.
However, a fine tooth hacksaw may be used. To prevent
a flare-out of the wire end during the cutoff operations,
wrap tape around the hose at the cutoff point. After the
hose is cut, and just prior to installing sockets, the tape
must be removed (see figure 4-50, detail A).
a twisting, pushing motion. Inserting sockets over neck
down end of hose will facilitate assembly. On extra long
assemblies. the sockets may be installed on each end of
2. Install sockets. Place two sockets
the hose individually (see figure 4-50, detail B),
skirt-to-skirt in a vise and work hose through sockets with
3. Size tube and flare braid. Place nipple
hex in vise. Push one end of hose onto the nipple and
work gently in circular motion to aid in separating the wire
braid from the tube. Remove hose from nipple (see figure
4-50, detail C)
(6) Assembly. High-pressure Teflon hose can be
assembled using the procedures provided in the follow-
ing paragraphs.
(a) Tools required. Use common hand tools,
i.e., wrench, hacksaw, protractor, vise, and hydraulic test
stand.
Change 3
4-69
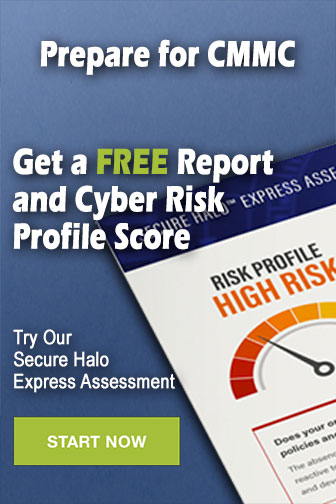