TM 1-1500-204-23-6
Table 6-3. Shelf Life of Adhesive
Storage
With catalyst
Without
With catalyst and
temperature
added
catalyst
promoter added
45°F ( 7°C)
6 months
When cement has been mixed
73°F (23°C)
3 days
4 months
with promoter and catalyst, it
104°F (40C)
12 hours
2 months
has practically no useful life at
122°F (50C)
2 hours
2 weeks
high temperatures and only
140°F (60C)
45 minutes
10 days
approximately 30 minutes life at
73°F (23°C)
e. Colored Cement. Colored cement is used for coating rubber parts for marking purposes. Brush application of
this cement is recommended, however, it can be sprayed or dipped on. Before application, clean the receiving surface
with aromatic naphtha, Federal Specification TT-N-97. After application, thorough evaporation of the solvent in the
cement is necessary for complete fuel resistance.
f.
Deicer Shoe Electrical Conducting Neoprene Surface Coat Cement. This neoprene rubber coating is used for the
resurfacing of deicer shoes when they become worn, scuffed, or bruised. It cures by solvent evaporation and is resistant
to ozone and sunlight. Best results are obtained by spraying, but it may be brush applied.
g.
General Purpose Synthetic Rubber Base Cement MIL-Spec MMM-A-1617. This cement can be used
successfully in a wide variety of applications, such as bonding vinyl to vinyl, rubber to rubber, rubber to metal, rubber to
fabrics, leather to leather, vinylite, wood, and metal surfaces it is suitable for use up to 158 °F (70°C) and has good water
and oil resistance and fair fuel resistance. It may be applied with a spatula or be brushed or sprayed when thinned with
methylethylketone, Federal Specification TT-M-261.
h.
Non-Hardening Distic Brand Cement. This cement is used specifically for cementing sanding disks due to its
nonhardening characteristics and the relative ease it provides in removing the sanding disk for replacement.
i.
Natural Rubber Adhesive, MIL-Spec MMM-A- 139, Class 3. This is a two-part, air drying, natural rubber adhesive
and is used for adhering natural or synthetic rubber and in particular for the manufacture and repair of articles fabricated
from natural rubber coated fabrics. These adhesives shall not be used for bonding nylon. It is used for permanent
repairs of pneumatic life rafts and life jackets.
j.
Neoprene Base Synthetic Rubber Cement. This two-part, self-curing, synthetic rubber cement is used in the
bonding of propeller anti-icer feed shoes. It can also be used for bonding neoprene, leathers, and porous materials to
themselves where oil and gasoline resistance is required. This cement is resistant to oil, gasoline, and water, is mildly
toxic and flammable. Check applicable maintenance manual for correct adhesive The following procedures should be
observed:
(1) Mix catalyst furnished with cement as soon as cement is opened.
(2) Apply cement with a brush. Working life of cement is 8 hours.
k.
Deicer Repair Cement. This two-part, water-resistant, modified gum rubber cement is used for making deicer
shoe repairs. It can also be used for making hot patches, cementing rubber to rubber, rubber-coated fabric to rubber,
and rubber to metal. The following procedures should be observed:
(1) Mix equal parts of each ingredient just prior to use, mixing only enough for 4-hour use.
(2) Apply by brush after surfaces have been slightly roughened and then cleaned with benzene, ASTM D836, or
nonleaded high-test gasoline. Apply one or more coats of mixed cement to each surface. Allow 30 minutes drying time
between coats. When final coat is dry, bring surfaces together and pressure cure for 20 minutes at 260 °F (126.7°C).
I.
Cement Primer. This solvent-type resinous solution is used in conjunction with neoprene base synthetic rubber
cement for bonding of propeller anti-
6-5
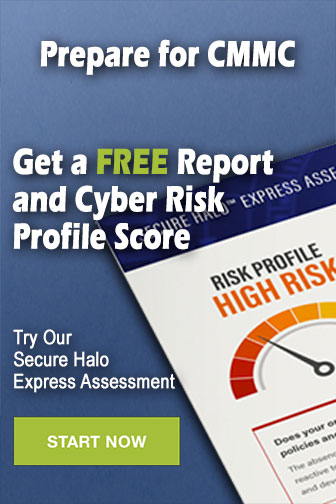