TM 1-1500-204-23-6
icer shoes. It can also be used as a primer for bonding iron, steel, chrome-plated and stainless steel, aluminum,
anodized or chromated aluminum, cured phenolics, acrylics, glass, wood, and concrete
(1) Roughening. Roughening the surface is sometimes found advantageous, particularly where solvent cleaning
has been found ineffective in removing mold release agents or other surface contaminants
(2) Applying. Apply by brush, spray, dip, roller, or flow coating.
(3) Drying. Allow a minimum drying time of 30 minutes before application of cement.
m. Composite Adhesives. Various adhesives and fasteners are used with composite materials. Refer to the
applicable maintenance manual for procedures concerning a particular aircraft. Adhesive curing time, application, and
shelf life vary with type of adhesive being used.
n.
Other Adhesives. Other adhesives, with various catalysts to permit different assembly periods and different
curing temperatures, are used extensively in aircraft fabrication. The storage life of these adhesives is very short, and
for this reason only small quantities should be carried in stock. These adhesives are equally suitable for attaching wood
or laminated plastic.
6-3. Sealants. Sealant characteristics and types are explained below. Sealants are classified as pliable, drying, or
catalyst cured sealants.
a.
Characteristics of Pliable Sealants. These sealants are referred to as one-part sealants, and are supplied ready
for use as packaged. They are solids and change little, if any, during or after application. Solvent is not used in this
type; therefore, drying is not necessary, and except for normal aging, they remain virtually the same as when first
packaged, neither hardening nor shrinking. The adhesion to glass, metal, and other impervious surfaces is excellent.
The adhesion is not complete until 15 to 30 minutes after it is applied.
b.
Characteristics of Drying Sealants. Sealants in this group set and cure by evaporation of the solvent. Solvents
are used in many of these sealants to provide the desired consistency for application. Once applied, however, the
solvent becomes an undesired constituent and must be eliminated to cause hardening of the sealant. Consistency or
hardness may change little or much when this type sealant dries, depending on the amount of solvent it contains. The
degree of shrinkage is dependent upon the proportion of solvents.
c.
Characteristics of Catalyst Cured Sealants. Catalyst cured sealants are transformed from a fluid or semifluid
state into a solid mass by chemical reaction or physical change. Air is not required to effect a cure. This type sealant
can be placed between faying surfaces. A chemical catalyst, or accelerator, is added and mixed just prior to sealant
application. Heat may or may not be employed. Temperature, and sometimes humidity, has a marked affect on life.
Temperature greatly influences cure time and heat is sometimes recommended as a means of shortening cure time.
d.
Sealing Compound, MIL-S-8784. Sealing compound, MIL-S-8784, is used in the sealing of integral fuel or oil
tanks. The sealant forms a low adhesion material, facilitating easy removal of fuel tank access doors and other
components. A feature of this sealant is that it will completely cure under fuel, therefore, fuel may be entered into the
tank upon completion of component installation. This is a two-part sealant available in two consistencies. Class A
consistency sealing compound is applied with a brush. Class B consistency sealing compound is applied with a putty
knife. Before applying sealant, ensure that surfaces are clean and free from grease. Class A and Class B are available
in either of two consistencies, A-1/2 or A-2, B-1/2 or B-2. The last dash number, -1/2 or -2, indicates the working
(application) time at room temperature.
e.
Sealing Compound, MIL-S-8802. Sealing compound, MIL-S-8802, is used in the sealing and repairing of integral
fuel and oil tanks. It can also be used for sealing pressure cabins, except where sealant would come in contact with
synthetic glass. This is a two-part synthetic rubber sealant available in two consistencies. Class A consistency sealing
compound is applied with a brush. Class B consistency sealing compound is applied with a putty knife, extrusion, or
injection gun. Mixing requires an accelerator, which reduces drying time. High temperatures further accelerate drying
time, thus reducing work life of the sealant. Application time at room temperature is given in table 6-4. The first coat
must cure to a tough, rubbery consistency before applying the cover coat. Tack-free cure time at room temperature is
given in table 6-5. Ensure that area to be sealed is clean and dry before applying sealant.
f.
Sealing Compound, MIL-S-7126. This non- hardening sealant is used for sealing synthetic glass. It can be used
as a filler for pressure cabin sealing Type I is a synthetic rubber putty. Type Ill is an extended type of putty consistency.
This sealing compound is applied by hand, putty knife, or extrusion gun. Working time is
6-6
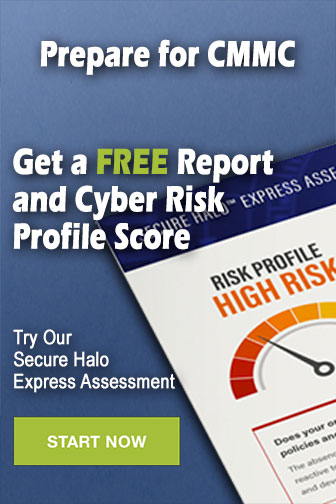