TM 1-1500-204-23-6
e.
Installation of Helical Insert. Installation procedures are as follows:
(1) Drill out stripped or damaged threads to minimum depth specified In table 2-15. The minimum depth
specified must be equaled or exceeded and will not include depth of countersinks, if any. Depth of
counterbores or countersinks, if any, will be in addition to minimum depth specified.
NOTE
Recommended minimum edge distance after drilling and tapping is nominal diameter of bolt, screw,
stud, etc., measured from centerline of tapped hole.
(2) Select tap of required nominal thread size and class fit from table 2-15. Tap threads using standard
thread tapping procedure.
(3) After tapping, clean out metal chips. Threads may be examined with a helical Insert gauge.
(4) Select correct size insert tool, either prewinder or sleeve type, from table 2-15. To use prewinder type
tool, pull back handle in sleeve until cutaway chamber is cleared of mandrel. Place insert in cutaway
chamber with tang toward threaded end of sleeve. Push handle forward so mandrel slot engages
insert tang. Turn clockwise, permitting Insert to engage In prewinder sleeve threads, and advance to
notch at opposite end of prewinder. Locate tool over tapped hole, and turn handle clockwise until
insert disengages from prewinder tool. Keeping mandrel in place, slide prewinder sleeve back toward
handle and turn Insert mandrel until insert is 1/4 to 1/2 turn below start of tapped thread.
(5) To break off tang for a through hole, select proper tang break-off tool from table 2-15. Place punch of
tool in insert and let It contact tang at bottom of hole. Strike top of break-off tool with sharp hammer
blow to snap off tang.
f.
Removal of Helical Insert. Removal procedures are as follows:
(1) Select proper size extract tool from table 2-15. Place tool blade into hole so that one side of blade is
1/4 turn from end of insert.
(2) Strike head of extract tool lightly with hammer.
(3) Bearing down on handle, turn slowly counterclockwise, firmly maintaining pressure as insert backs out.
NOTE
Proper removal of insert does not damage tapped threads.
g.
Installation of Twinsert. Installation procedures for Twinsert are as follows:
NOTE
Because the Twinsert tapped hole and the free diameter of the Twinsert are larger than for the
corresponding size insert, the recommended insert tool for the Twinsert is different from the insert tool for
the screw thread or screw lock insert. Part numbers of recommended tools for each size Twinsert are in
table 2-16.
(1) Drill minor diameter within minimum and maximum specifications. Drill depth to the same as for
original insert (see figure 2-66).
(2) Tap thread for Twinsert. Full tapped thread length is to be same as for original insert.
(3) Remove chips.
(4) Install Twinsert 1/4 to 1/2 pitch below top surface with insert tool.
(5) Break off Twinsert driving tang with break-off tool
(6) Install screw thread or screw lock insert to position where end of insert is flush with end of Twinsert,
using screw thread or screw lock insert tool.
(7) Break off insert driving tang with break-off tool.
h.
Removal of Twinsert. This procedure is the same as that for removal or regular screw thread lock inserts.
That is, by use of an extract tool, or if space permits and the tang Is intact, by rotating the insert forward
through the hole, using insert tool mandrel. Refer to table 2-16 for extract tool numbers.
2-62
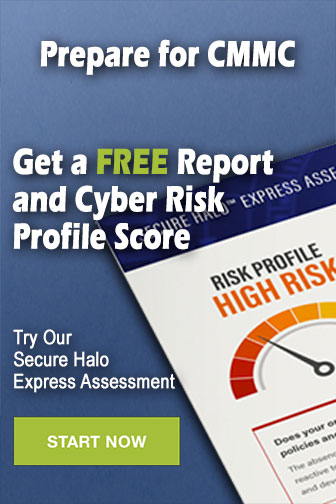