TM 1-1520-264-23
4.31.4
Backup Method. None required.
4.31.5
System Securing. Clean the main landing gear mount shaft thoroughly to remove all residual magnetic
particle media. Refer to Post Cleaning and Restoration of Part or Area After NDI, paragraph 1.4.16. The main landing
gear shock strut requires installation in accordance with the applicable technical manuals listed in Table 1-1.
4.32 TAIL LANDING GEAR FORK (ET).
4.32.1
Description (Figure 4-1. Index No. 32)
. The tail landing gear fork holds and attaches the tail wheel to the
helicopter by means of a shaft to the tail landing gear trailing arm assembly.
4.32.2
Defects. Defects can occur anywhere on the surface of the tail landing gear fork. No cracks are allowed.
4.32.3
Primary Method. Eddy Current.
4.32.3.1
NDI Equipment and Materials. (Refer to Appendix B )
a.
Eddy Current Inspection Unit
b.
Probe, straight, shielded surface, 100 KHz-500 KHz
c.
Probe, right angle, shielded surface, 100 KHz-500 KHz, 90
°
1/2 inch drop
d.
Cable Assembly
e.
Reference Block, three-notched aluminum (0.008, 0.020, and 0.040 EDM notches)
f.
Teflon Tape, refer to Table 1-8
g.
Aircraft Marking Pencil, refer to Table 1-8
4.32.3.2
Preparation of Helicopter. The helicopter shall be prepared for safe ground maintenance. A partial inspection
for cause (visual indications, sites of mechanical damage, corrosion, etc.) may be performed on all exposed surfaces of
the installed part using this procedure. If required, the tail landing gear fork shall be removed in accordance with the
applicable technical manuals listed in Table 1-1.
4.32.3.3
Access. Not applicable.
4.32.3.4
Preparation of Part. The part shall be thoroughly cleaned. Refer to Preparation of Part or Area for NDI,
paragraph 1.4.4.
4.32.3.5
NDI Equipment Settings.
a.
Make the following initial settings on the Eddy Current Inspection Unit, NORTEC-19e
11
Frequency F1
- 200 KHz
F2 - off
HdB
- 57.0
VdB
- 69.0
Rot
- 56
Probe drive
- mid
LPF
- 100
4-72
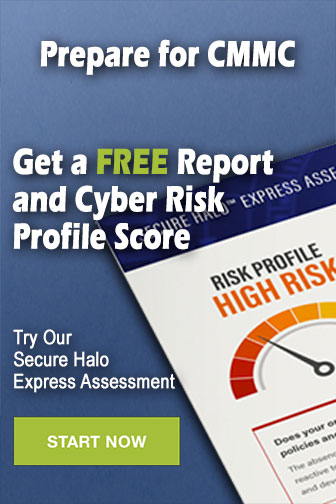