TM 55-4920-428-13
d. Power supply on TB6A provides the +20 volts dc, 20 volts dc, +33 volts dc, and 33 volts dc. These dc
voltages are used in the BITE circuit. They are also used to power the servo amplifiers.
e. Power supply PS1 provides the +12 and 12 volts dc. This power supply also includes a 5 volts dc regula-
tor powered from the +12 volts supply. The +12 and 12 volts dc are used in the BITE and ILCA control cir-
cuits. The 5 volts dc powers the DVM,
f. The +7 and -7 volts dc are obtained from zener diode circuits that are powered from the +12 and -12
volts dc respectively. The +7 and 7 volts dc power the NOR gates and the demodulators.
g. LAMP TEST switch S11 is pressed to check all tester light bulbs. When S11 is pressed, K1 and K2 are en-
ergized, supplying dc voltage to all bulbs.
1-20. Under-voltage Detector Circuit TB-6B (fig. 1-8).
a. The undervoltage detector circuit samples line voltage at transformer TB6T1. A reduced sample is applied
to the input of comparator U1. When the positive peak of ac voltage is higher than the threshold voltage, the
comparator output is a low.
b. When line voltage is above 105 volts, the comparator provides a series of low pulses. When line voltage is
below 105 volts, the comparator output at pin 8 goes high enough to turn Q1 on. With Q1 on, there is a ground
path and the WARNING indicator is turned on.
c. When the line voltage goes back above 105 volts, U1 pin 8 output goes low. The low from pin 8 turns off
transistor Q1.
d. This interrupts the ground path and the WARNING indicator light will be off. R10 is used to adjust the
undervoltage detector threshold voltage level.
e. When LAMP TEST switch S11 is pressed, +dc voltage is applied through R9 to pin 10 of U1. This causes
output pin 8 to go high and energize Q1, turning on the WARNING light.
f. When LAMP TEST switch S11 is released, the first positive pulse at pin 9 makes the pin 8 output go low,
turning Q1 off.
g.
That removes the ground path and the WARNING indicator will be off.
1-21. Hydraulic Unit Control Circuit (fig. 1-9). The hydraulic unit control circuit includes SOLENOID
SHUTOFF switch S18, CYCLE MOTOR switch S12, and relay K2.
a. When the SOLENOID SHUTOFF switch is pressed to CLOSED, 28 volts dc is applied through the A con-
tacts. The dc lights the CLOSED indicator. When the SOLENOID SHUTOFF switch is pressed to OPEN, 28
volts dc is applied through the A contacts. The dc lights the OPEN indicator. At the same time, 115 volts ac is
applied through the B contacts to the hydraulic unit. When the SOLENOID switch S1 is closed, 115 volts ac
lights OPEN indicator S1 and energizes the hydraulic solenoid.
b. When the CYCLE MOTOR switch is pressed to OFF, 28 volts dc is applied through the A contacts to
light the OFF indicator. When the CYCLE MOTOR switch is pressed to ON, 28 volts dc is applied through the
A contacts to light the ON indicator. At the same time, 115 volts ac is applied through the B contacts to operate
the cycle motor.
c. Relay K2 operates when LAMP TEST switch S11 is momentarily pressed (fig. 1-7). The 28 volts dc is ap-
plied through the relay contacts to light OPEN, CLOSED, ON, and OFF indicators. When the LAMP TEST
switch is released, relay K2 is deenergized. One indicator in each switch goes out.
1-22
Change 3
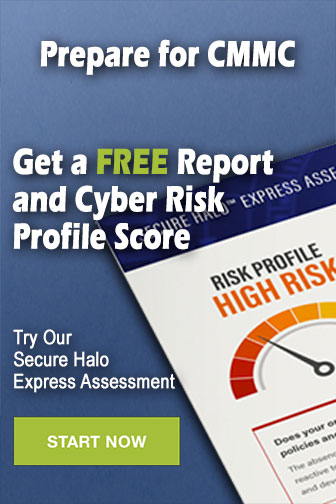