TM 1-1500-204-23-1
(a)
Open curing agent Pro-Seal 890A
and thoroughly mix it In the container until it becomes a
smooth paste.
(b)
Thoroughly mix 10 parts of Pro-Seal
890A to 100 parts of Pro-Seal 890 by weight, or 8.4 parts
of Pro-Seal 890A to 100 parts of Pro-Seal 890 by volume.
(c)
Carefully fold the material upon itself
and blend for a period of at least five minutes This will
give a satisfactory mix.
NOTE
Avoid violent agitation In order to beat
as little air Into mixture as possible
Also, frictional heat developed from
violent agitation may reduce work life
of the material.
(5)
Curing requirements for Pro-Seal 890
sealant (2 cure option). Requirements are as follows:
Mixed, uncured Pro-Seal 890 sealant material
(Class A-2 or B-2) requires 72 hours at room
temperature for a full cure.
If the production schedule is not flexible enough
to allow for the long-time room temperature
cure, accelerated step curing conditions may be
employed to fully cure the sealant material In
four hours at elevated temperatures The step
curing conditions are two hours at 120 °F
(49°C), followed by an additional two hours at
158°F (70°C). This means that you should use
two ovens set at the two different temperatures
specified to fully cure the uncured material
under accelerated conditions.
d.
Repair of Armor Plating. Specific repairs and
Inspections for armor plating are described in the
following paragraphs.
(1)
Repair and inspection of cracked tile Repair
and Inspection procedures are as follows:
(a)
Inspect for cracked tiles.
NOTE
Multiple cracks converging at an angle
of
15
degrees
or
less
are
not
repairable. You may repair cracks
occurring in the ceramic tile 1/16 of an
inch or less In width, provided that the
backing
Is
not
damaged
beyond
repair. Do not repair armor panels
where a crack (or cracks) wider than
1/16 if an Inch is found. Total
allowable defects are three or less
cracks, chips, or spalls in any 2-inch
square area.
(b)
Repair cracked tile by bonding a 1/8 inch
thick sheet of fiberglass, type GEE, MIL-P-18177, over
the crack (or Cracks) overlapping the damaged area by
three (3) inches on each side, using Polysulfide Sealant
Pro-Seal 890 (FSCM 83527).
(c)
Bevel all edges of the fiberglass patch 1/4
Inch deep and 30 degrees from the top surface so the
nylon spa shield will fit smoothly over the patch.
NOTE
For ceramic having raised edges at the
joints, one side of the patch may be
cut short of the 3 inch overlap
requirement. If the crack extends
through a raised edge on the tile,
shape the patch, by undercutting, to fit
over the raised edge. Use good
judgment in determining this, bearing.
In mind that the patch is to restore
structural integrity of the panel When
patching along a panel edge, cut patch
to
fit
the
edge
boundary
along
periphery of the tile.
(d)
Remove existing sealant residue from
the tile surface by using a solution consisting of 50
percent by volume of Petroleum Distillate Base, TT-T-291
and Toluol, TT-T-548.
(e)
Lightly abrade the fiberglass patch
and ceramic surface surrounding the cracked area where
the patch (or patches) is to be bonded.
(f)
Clean the abraded ceramic and patch
surface using a clean cloth moistened with methyl ethyl
ketone, TT-M-261. To obtain satisfactory adhesion, apply
sealant only to a clean dry surface, free of oil and grease.
9-51
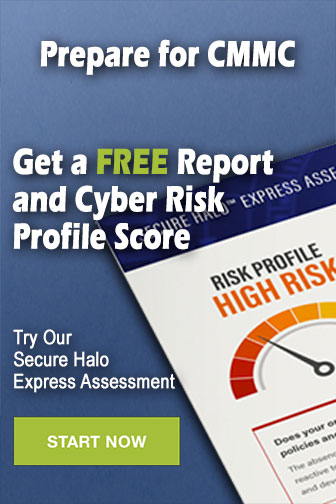