TM 1-1500-204-23-1
(c)
Attaching equipment damage. Repair
attaching equipment damage as follows.
1 Repair, when practicable, or
replace all damaged attaching equipment such as straps,
buckles, webbing, keepers, cords, cables, cable fittings,
grommets, etc.
2 Dip ends of all new webbing in
a mixture of 50 percent paraffin, Federal Specification
VV-W-95, and 50 percent beeswax, Federal Specification
C-B-191
3 Dip ends of sash cords In
shellac, Federal Specification TT-S-271.
(3)
Waterproofing. Restore water, mildew, and
weather resistant qualities of a protective cover by coating
with water repellent textile finish compound as follows
WARNING
Solvents
contained
in
the
compounds are highly flammable
and toxic; therefore all work shall be
accomplished In an open area away
from any flame
(a)
Stir
compound
thoroughly
until
uniform mixture is obtained.
(b)
Spread cover out completely on a
clean flat surface, with Inside of cover down.
WARNING
Solvents contained In compound may
tend
to
irritate
skin,
therefore,
prolonged contact shall be avoided.
(c)
Apply
moderate
application
of
compound to outside of cover with a brush or spray.
(d)
Apply compound well into seams, as
they are particularly susceptible to mildew and leakage
(e)
Dry cover thoroughly until odor of
compound has completely disappeared
(4)
Storage. Store protective covers as
follows:
(a)
Fold covers neatly to facilitate easier
and faster installation when covers are needed.
(b)
Store covers in a dry place on a
platform or on slats of wood. Never store covers on
ground or concrete.
9-23. Armor Plating. The repair instructions that follow
are limited to composite armor composed of a ceramic
facing bonded to a fiberglass reinforced plastic backing.
The ceramic facing is covered with a flexible spall shield
to protect the crew members from ballistic fragments. A
rubber molding is also provided on the edges of some
panels for crew protection. These repair procedures were
developed with the objective of matching, to a high
degree, the original strength and ballistic properties of the
undamaged armor panel, with a minimum increase in
weight. Extending the service life of armor panels will
facilitate the mission capabilities of organizational units by
the effective use of material assets. The ceramic facing
may consist of one of the following materials.
Aluminum Oxide (AI203)
Boron Carbide (B4C)
Silicon Carbide (SiC)
a
Armor Plating Inspection and Repair Definitions.
Table 9-6 gives definitions relative to inspection and
repair criteria.
b.
General
Inspection
of
Armor
Plating.
Radiographic inspection of the assembled armor panel is
the primary method used for nondestructive testing in
determining the extent and location of internal damage.
The radiographic skills and equipment required for this
type of testing, while available at Depot installations, are
not available to Army field units. Therefore, for field
units, a visual inspection of the panels must be made,
which requires removal of the nylon spall shield. Remove
the edge molding and peel off the nylon spall shield.
Exercise care when removing the spall shield to avoid
damage to the cloth. Use the following inspection
procedures.
CAUTION
Handle
armor
panels
with
care.
Ceramic tile is brittle and cracks
easily.
9-48
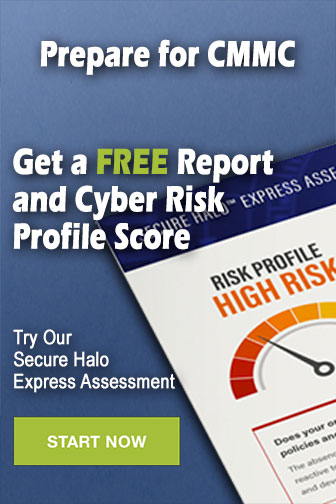