TM 1-1500-204-23-1
(d)
Place filter on a 25-degree angle
draining rack in a room where temperature is 70 °F
(21°C) and allow to drain for 2 to 4 hours. Drain
accordion-pleated filters for 8 hours.
(e)
When
necessary,
use
forced
draining after gravity draining has been accomplished
by using a 1/16-inch orifice and 100 psi air temperature.
(5)
Adjust carburetor air doors so they
operate freely through full range of travel or to position
selected as specified in applicable maintenance manual.
(6)
Replace damaged intake pipes. Detect
leaks in Intake pipes by presence of fuel stains at
cylinder Impeller end When leakage is found after 25
hours of operation (since new), loosen intake pipe
packing nuts. Replace any defective packing and
retighten nuts.
NOTE
Do not tighten packing nuts without
loosening
and
examining
the
packing first.
b.
Turbocharger and Supercharger Maintenance.
Visual inspection of all visible parts should be
accomplished daily to observe oil leaks, exhaust leaks,
cracks in the metal of hot sections, loose or insecure
units, and other unacceptable conditions. Refer to the
applicable
maintenance
manual
for
specific
maintenance procedures. Ensure the following Items
are checked.
· Mounting of all units
· Oil leaks or dripping from any unit
· Security of oil lines
· Security and condition of electric wiring
· Cracks in ducting and other metal parts
including the turbine and housing
· Warping of metal ducts
· Operation of the complete system to
determine
performance
to
discover
undesirable sounds, and to note evidence of
vibration; unusual sounds and appreciable
vibration require removal and replacement of
the turbocharger to correct the faulty condition
NOTE
Exhaust ducts, waste gates, nozzle
boxes, and turbines are subjected to
extremely high temperatures. For
this reason, cracks develop because
of the continued expansion and
contraction
of
the
metal
as
temperature changes occur.
7-8. Exhaust System. The exhaust system conducts
exhaust gases from the engine to the atmosphere with
minimum exhaust back pressure. Short exhaust stacks
are incorporated on some engines, while others join a
collector ring which expels exhaust gases through a tail
pipe. Perform the following general maintenance
procedures on exhaust systems:
a.
Check ball joints for excessive or insufficient
clearances, and retighten or replace ball joints as
necessary to obtain free movement.
b.
Replace all parts that have hot spots or damage
beyond repair.
c.
To prevent exhaust port studs from seizing, and
to retard corrosion, apply a special lubricant as follows:
(1)
When engine or cylinder is removed or
installed, apply light coating of 10 percent molybdenum
disulphide lubricant, MIL-M-7866, and 90 percent
grease, MIL-G-3545, to threads of cylinder exhaust port
studs.
(2)
To retard corrosion of nuts, apply this
mixture to exterior of exhaust port stud nuts.
d.
Tighten all nuts, bolts, and clamps in exhaust
system in accordance with maintenance manual for
engine involved.
7-9. Carburetion and Fuel Injection. Fuel is metered
to the engine at a predetermined ratio to airflow by the
fuel metering system. Fuel metering systems differ in
design, but their function is the same, regardless of type
or engine model. Improper maintenance of the fuel
metering
system
will
result
in
rough
engine
performance, detonation, spark plug fouling, low power
output, poor acceleration, and engine or part failure.
a.
Inspection. Inspect carburetors for mounting
flange cracks and evidence of leakage and fuel strainers
for foreign matter broken screens, corrosion, and
distortion.
7-36
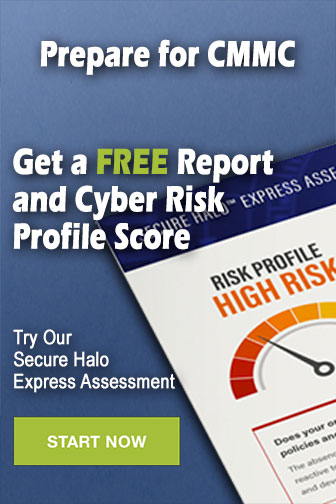