TM 1-1500-204-23-2
KZ5330-833-7491
PACKING PERFORMED SYN RUBBER
1 EACH (MS287785)
DISC-38329
A-5/80
SR 810-B-90
MFD DATE 4:80, CURE DATE 2080
STILLMAN RUBBER CO (MFGR/ CONTR)
MIL-G-5510A
Figure 4-59. O-Ring Identification
(3) Removal. When removing O-rings, care must be taken to ensure that the groove surface is not marred or
scratched (see figure 4-60) The correct tool should be used In order to minimize this kind of damage. A variety of these
tools may be used on any given job. They should be made from soft metal such as brass and aluminum, however, tools
made from phenolic rod, plastics, and wood may also be used. Avoid using pointed or sharp-edged tools that might
damage the O-ring
(a) Removing internal O-rings During removal of O-rings, the hook type removal tool is put under the O-ring and
then lifted to allow the extractor tool to pull the O-ring from its place See figures 4-61 through 4-64 for removal of various
configurations of O-rings
(b) Removing external O-rings. It is less difficult to remove external O-rings than internal ones. Two accepted
removal methods are described In the following paragraphs
1 Spoon-type extractor. A spoon-type extractor is positioned under the seal, as shown in figure 4-65 After the
O-ring Is taken from Its cavity, the spoon Is held still while the piston is rotated and withdrawn.
2 Wedge-type extractor. A Wedge-type extractor tool Is inserted under an O-ring as shown In figure 4-66, and
the hook type removal tool hooks the O-ring A slight pull on the hook removes the O-ring from its cavity
(4) Installation O-rings, as a rule, require no adjustment In installation, but the precautions described In the following
paragraphs must be observed or early failure will result.
(a) Cleaning. After all O-rings are removed, cleaning of the parts that will receive new O-rings is mandatory Ensure
that the area used for such Installations is clean and free from all contamination
(b) Inspection. Each replacement O-ring should be removed from its sealed package and Inspected for defects such
as blemishes, abrasions, cuts, or punctures. Although an O-ring may appear perfect at first glance, slight surface flaws
may exist These can prevent satisfactory O-ring performance under the variable operating pressures of aircraft systems
O-rings having flaws that will affect their performance should be rejected
(c) Sizing. Ensure that O-ring Is of proper size. Uniform pressure on O-ring In Installed position is necessary for
satisfactory operation
WARNING
O-ring splicing and O-ring assortment kits do not meet the specific requirements for O-ring usage on
aviation equipment and are not authorized for use on Army aircraft. Use of unauthorized O-rings may
compromise the integrity and safety of equipment and personnel
CAUTION
Never use adhesive tapes to cover danger areas on components. Gummy substances left by the
adhesives are extremely detrimental to hydraulic systems.
(d) Installation. Immerse rings to be installed in hydraulic systems in hydraulic fluid, MIL-H5606 or MIL-H-83282.
During installation, avoid rolling and twisting the O-ring to put it Into place If possible, keep the position of the O-ring
mold line constant. After the O-ring is placed In the cavity provided, gently roll the O-ring with the fingers to remove any
twist that might have occurred during Installation. When the O-ring installation requires spanning or Inserting through
sharp threaded areas, ridges, slots, and edges, use protective measures such as the O-ring entering sleeves shown In
figures 4-67 through 4-69. If the recommended O-ring entering sleeve (soft thin-wall metallic sleeve) is not available,
paper sleeves and covers may be made by using seal package (gloss side out) or lint-free bond paper
4-81
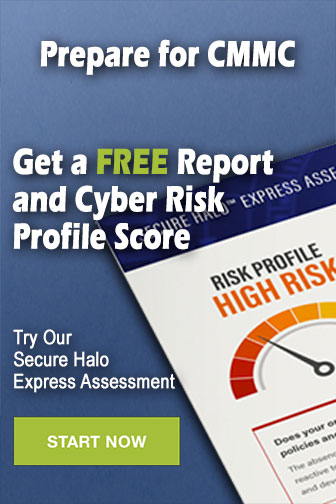