TM 1-1500-204-23-2
may have excessive motion restrained where necessary, but should never be rigidly supported.
f.
Chafing. Eliminate chafing by using suitable bulkhead-type grommets or cushioned clips and ensuring
adequate clearance.
g.
Temperature Protection. Protect hose installation from excessive temperature such as exhaust blasts,
supercharger ducts, and the like, by either shrouding or relocation. Use of flame-resistant hose is preferred forward of
firewall as this area is subject to high temperature under certain conditions.
h.
Hose Connections to Engines. Where hose connections are made to engines or to engine-mounted
accessories, install hose so 1 1/2 inches of slack or an adequate bend is provided between last point of support and
attachment to engine or accessory. This prevents possibility of hose being pulled off nipple due to engine movement.
i.
Hose Clamp. When a length of hose is connected to engine with a hose clamp, support hose firmly to
prevent vibrational and torsional strain on hose connection. When possible, place support approximately 3 inches from
engine connection.
j.
Hose Markings. When possible, install hose so all markings on hose are visible.
k.
MS Flared Swivel Connectors Torquing. Torque MS flared swivel connectors in accordance with tables 4-33
and 4-34.
Table 4-32. Minimum Bend Radii of Hose for Fuel, Oil, and Coolant Systems
Hose (Military
Specification No.)
Size
Correct radii
MIL-H-8794
All
See MS33790
MIL-H-7061
Up to and
R = 6 x inside
including
diameter
1 1/4 inch
inside
diameter
MIL-H-7061
Larger than
R = 12 x inside
1 1/4 inch
diameter
inside
diameter
MIL-H-5593
All
R = 12 x inside
diameter
MIL-H-6000
All
R = 12 x inside
diameter
MIL-H-7938
All
R = 12 x inside
diameter
4-77
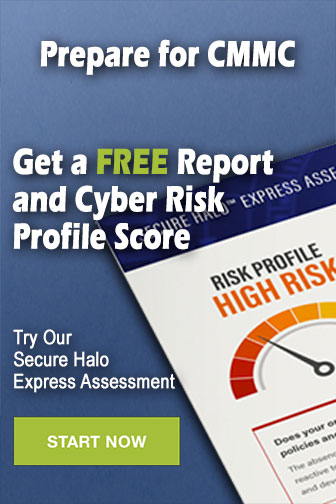