TM 1-1500-204-23-2
inward. Fluid moving of the actuating unit as the piston moves Inward flows into the return line to the reservoir.
c.
Pneumatic System. Aircraft pneumatic systems are mostly used as an emergency source of pressure for
hydraulically operated subsystems. The pneumatic power system usually consists of one or more high pressure air
cylinders, pressure gauges, and pressure warning lights. Since the pneumatic power source does not replenish itself
during flight, the compressed supply is good for only a certain number of operations.
(1)
Construction. High pressure pneumatic systems are constructed to operate in much the same
manner as hydraulic systems. A shuttle valve connects the pneumatic system to the hydraulic system. This allows the
use of the same tubing and units for both systems. The shuttle valve separates the normal hydraulic system from the
pneumatic system. Pneumatic system selector valves control the air to the subsystems. Each subsystem is connected
to the high pressure air source through a pressure regulator and relief valve assembly and a selector valve. Since
pneumatic selector valves are installed in parallel, air pressure is Immediately available to all subsystems for instant
operation. Connected in this manner, more than one system can be operated at the same time.
(2)
Servicing. The air cylinders are charged through a ground test filler connection by a portable
nitrogen cart or a high pressure air compressor. All nitrogen or air is filtered by a filter in the service line.
4-18.
Aircraft Brake Systems. All hydraulic brake systems operate on the same basic principle. When the operator
moves a brake pedal or other brake operating control, the movement is transmitted to a master cylinder or to a power
brake control valve from which fluid pressure is delivered through connecting lines to a brake assembly connected to a
wheel or shaft whose movement is to be braked. The fluid pressure acting on the brake assembly pushes brake linings
Into contact with surfaces of a rotating disc. The resulting friction slows--and finally stops--the continued rotation of the
wheel or shaft to which the disc is connected. When the brake pedal or brake control is returned to the off position, brake
operating pressure is relieved, the brake lining loses contact with the disc, and the wheel or shaft is free to turn again.
a.
Wheel Brake Systems. Aircraft wheel brake systems are dual in nature in that they are composed of two
identical subsystems that can be operated independently of each other to provide separate braking action for the landing
gear on each side of the aircraft. Each subsystem is operated by a toe plate (brake pedal) that is hinge-mounted to the
top of the aircraft rudder pedal. Since each brake pedal can be operated independently the brakes can be used for
steering the aircraft. A list of components, which may be found in varying combinations to make up the different wheel
brake systems, includes the following: master cylinder (or a power brake control valve), wheel brake assemblies
deboosters, parking brake valves, shuttle valves, accumulators, connecting lines, and bottles charged with compressed
air. The minimum number of parts which could be used to perform the function of a simple wheel brake system are a
master cylinder (or a power brake control valve), a wheel brake assembly, and connecting lines.
(1)
Master cylinders. Master cylinders are used in some wheel brake systems as the means of
transforming force applied by the of the operator foot into fluid pressure; the greater the force applied to the pedal, the
higher the fluid pressure. Master cylinders fall into three general classifications: simple, compound, and powerboost.
Within these classifications, there are many variations in shape, size, and design, depending on the manufacturer and on
how the cylinder functions in the brake system. Brake systems incorporating simple and compound master cylinders
operate independently of any other hydraulic system within the aircraft and are sometimes called independent brake
systems. In brake systems using a power boost master cylinder, some of the power needed for braking is supplied by a
power-driven pump.
(a)
Simple master cylinder. Some simple cylinders have integral reservoirs; others are
connected with in-line reservoirs by means of a hose. In some designs, a push rod actuates the piston; in others a pull
rod performs this function. The design shown in figure 4-148 has an integral reservoir, and the piston is actuated by a
push rod. Note that the illustration shows the cylinder in released position, with the compensating valve open. This
allows any thermally expanded fluid within a connected wheel brake assembly to pass freely into the reservoir and from
the reservoir back into the assembly to replace fluid that may have been lost due to minor leakage. When the brake
pedal is depressed, the first few thousandths of an inch of travel of the master cylinder push rod closes the compensating
valve, thus trapping the fluid that lies between the underface of the piston and the wheel brake assembly. Further
depression of the brake pedal moves the piston within its bore and forces fluid out of the master cylinder
4-143
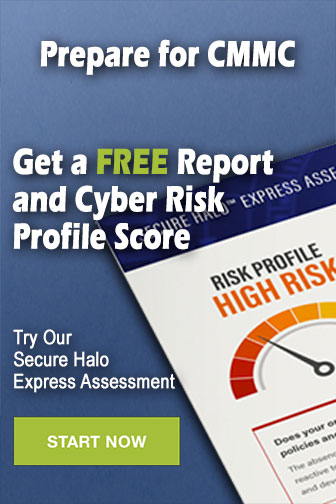