TM 1-1500-204-23-2
CHAPTER 4
HYDRAULIC MAINTENANCE PRACTICES
4-1. General. This chapter provides general instruc-
tions for maintenance of aircraft hydraulic systems, the
materials required, and methods to be used. A systemat-
ic application of the basic information in this chapter will
result in more efficient maintenance practices. In those
cases where specific instructions for a particular aircraft
are required, refer to the applicable aircraft maintenance
manual. Materials and processes recommended are
identified by military or federal specification number or by
manufacturer.
4-2. Tubing Systems and Repairs. Tubing used in
aircraft hydraulic systems carries pressure to distant
points in the aircraft to provide control of various critical
components. Failure of this tubing will result in pressure
loss and subsequent loss of control, resulting in possible
destruction to aircraft and injury or death.
a.
Types. Corrosion-resistant steel tubing and alu-
minum alloy tubing are used in aircraft for fuel, oil, cool-
ant, oxygen, instrument, hydraulic, and vent lines, as well
as for electrical conduits and ventilating ducts. Copper
tubing generally has been superseded as a general pur-
pose tubing by aluminum alloy tubing because of its light-
er weight, ease of forming, and resistance to corrosion
and fatigue. Tubing material can be identified by visual
inspection or by the aluminum alloy designation stamped
on the surface.
(1) Corrosion-resistant steel tubing. Corrosion-
resistant steel tubing, MIL-T-8504 and MIL-T-6845, is
used in high pressure hydraulic systems (3000 psi) such
as landing gear, wing flaps, and brakes. External brake
lines should always be made of steel to prevent damage
caused by flying gravel and stones and ground handling
accidents. On hydraulic systems using 1/2-inch corro-
sion-resistant tubing or larger, aluminum alloy nuts and
sleeves may be used. Steel nuts and sleeves should be
used on 3/8 inch corrosion resistant tubingor smaller.
Corrosion-resistant steel tubing does not have to be an-
nealed for flaring or forming. The flared section is some-
what strengthened by cold working and consequent
strain hardening. The high tensile strength of corrosion-
resistant steel tubing permits use of thinner walls than
those of aluminum alloy tubing, but the weight is about
the same as thick-walled aluminum alloy tubing.
(2) Aluminum alloy tubing. Aluminum alloy tub-
ing, Federal Specification WW-T-700/1, is used for gen-
eral purpose lines and conduits of low fluid pressure,
such as instrument lines, and electrical and ventilating
conduits. Aluminum alloy tubing Federal Specifications
WWT-700/4 and WW-T-700/6, is the most widely used
tubing for general purpose lines of low and medium pres-
sures. It is easily flared, and is soft enough to be formed
with handtools. It should be handled with care to prevent
scratches, dents, and nicks. Aluminum alloy tubing is
used with either of two types of connections; flared joint
for mechanical connections, or beaded end for use with
clamps and flexible hose connections. In hydraulic sys-
tems, 5052-0 aluminum alloy tubing, Federal Specifica-
tion WW-T-700/4, is used for reduced pressure (1500 psi
maximum) and return lines. Aluminum alloy tubing 6061
and 6062 MIL-T-7081, may be used for high pressure
lines (3000 psi). Use of MIL-T-7081 tubing in aircraft is
limited by MIL-H-5440. Tubing conforming to Federal
Specifications WW-T-700/1 and WW-T-700/6 shall not
be used in hydraulic systems.
(3) Copper tubing. High pressure oxygen sys-
tems use 3/16-inch diameter, 0.032-inch wall thickness
copper tubing, Federal Specification WW-T-799, Type N.
Fittings are silver soldered onto the tubing in accordance
with MIL-B-7883, before tubing is installed.
(4) Rigid Tubing. The tubing used to produce
rigid tubing assemblies is sized by its outside diameter
(OD) and wall thickness. Outside diameter sizes are in
sixteenth-of-an-inch increments, the number of the tube
indicating its size in sixteenths of an inch. For example,
the number 6 tubing is 6/16 or 3/8 inch, number 8 tubing
is 8/16 or 1/2 inch, and so forth. Wall thickness is speci-
fied in thousandths of an inch. Most aircraft maintenance
manuals contain a table which lists the original material
and acceptable substitutes and gives the wall thickness
for each.
b.
Tubing Identification. The Army uses two types
of identification systems to code hydraulic plumbing lines
of aircraft. The two systems used are the printed-symbol-
ized tape system (see figure 4-1), the preferred method,
and the solidcolor band (see figure 4-2), the alternate
method. This identification will be applied in accordance
with TM 1-1500-204-23-1) paragraph 6-3.
c.
Tubing Damage. Damage such as nicking and
scratching of tubing can be minimized by using care.
Most damage of this kind occurs from careless handling
of tools during maintenance of aircraft. Any dent less
than 20 percent of tubing diameter is not objectionable
unless it is on the heel of a short bend radius. A nick no
deeper than 15 percent of wall thickness of aluminum,
aluminum alloy, copper, or steel, and is not in the heel of
the bend, may be reworked by
Change 3 4-1
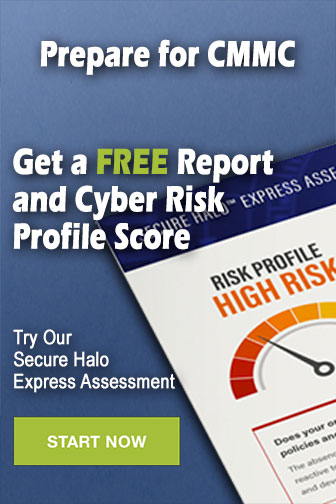