TM 1-1500-204-23-2
have a radius for 1/4-inch and 3/8-inch tubing. All sizes above 3/8 inch will require the use of a mandrel to form. Bends
in 5/16 inch outside diameter oxygen tubing should have a radius or curvature of at least 11/16 inch. Tubing may be
bent without the aid of tools by carefully forming desired radius by hand; however, this method is crude and should be
used only in absence of proper tools. Aluminum alloy tubing used in oxygen systems should not be hand bent. Tubing
1/2 inch outside diameter or larger should be packed with fusible alloy, Federal Specification QQ-F-838, to prevent
cracked or wrinkled bends. When bending tubing, a large radius should be formed and gradually worked down to desired
radius.
CAUTION
A torch or flame should never be applied to tubing or fusible alloy, as excessive heat will destroy both
strength of heat-treated tubing and melting characteristics of fusible alloy. Boiling water will not melt
fusible alloy after a flame has been applied.
(1)
Use of fusible alloy for bending tubing. A bending machine should be used when bending aluminum or
duralumin tubing. Before bending, most aluminum alloy tubing is in annealed condition, and should be packed with
fusible alloy, Federal Specification QQ-F-838. One end of tube to be bent is closed to prevent leakage of fusible alloy.
Tubing and ladle containing fusible alloy is immersed in a tank of boiling water until alloy is melted. Melting point of the
fusible alloy is 160 degrees (71 degrees C). For ordinary tubing lengths, a hot water tank similar to that used in plating
shops may be used. For longer lengths, a special tank may be constructed, or a length of pipe used so that both tubing
and ladle will be completely submerged. When fusible alloy has melted, it is poured into tubing. Both tubing and ladle
are kept beneath surface of hot water during pouring operation so that molten alloy will displace water in tubing. Remove
tubing from hot water and cool with cold water or allow to air cool until fusible alloy is solidified. Tubing can then be bent
with a bending machine or form blocks. Fusible alloy should be cold when bending tubing, and tubing should be bent
slowly. When bending operation is completed, fusible alloy may be removed from tubing by immersing both tubing and
ladle in tank of hot water and pouring alloy back into ladle. When pouring alloy back into ladle, both tubing and ladle
should be kept beneath surface of hot water, as this reduces tendency of alloy to stick to inside of tubing.
(2)
Tube flattening. In some cases, a certain amount of flattening may occur when bending tubing
regardless of procedure used, especially on thin-walled tubing bent to minimum bend radii. As tube flattens, it assumes
the shape of an ellipse in cross section, and the area is reduced. This restriction either reduces amount of fluid actually
delivered, or requires additional pumping power to overcome increased line friction. When tube is flattened so that minor
axis of ellipse is 75 percent of normal tube diameter, area is reduced to 90 percent of original. Further flattening of tube
may be considered as cause for rejection.
(3)
Tube bend data drawing. Tube bend data shall be prepared on A size drawings in accordance with
format shown in figure 4-6. Local forms for tube bend data are no longer acceptable. Points of possible confusion are
explained in the following paragraphs.
(a)
Distance from Y end. DISTANCE FROM Y END column shows the measured distance from the
Y end to the first bend, the measured distance from Y end to the second bend, etc. This distance can be measured
either by making all measurements before any bending takes place, or by utilizing scale on the bending machine.
(b)
Dial setting. DIAL SETTING column shows degree of bend from the horizontal reference plane.
This column is based on a 360-degree graduated dial for the bending machine. Where a dial is graduated in 180
degrees, right and left indications are used, and it is necessary to compute necessary setting for settings more than 180
degrees. This calculation consists of subtracting the dial setting shown from 360 degrees. Result will be proper setting
for left side of dial. Dial settings less than 180 degrees are identified for both types of dials. For continuity of operation,
dial settings are based on continual clockwise rotation of dial.
NOTE
Example: For a desired dial setting of 286 degrees, the reading on a 360-degree dial is 286 degrees. To
determine the reading on a 180 degree dial for a dial setting of 286 degrees, subtract 286 degrees from
360 degrees. The difference (74 degrees) is the reading as read on the left side of the dial.
Change 1 4-3
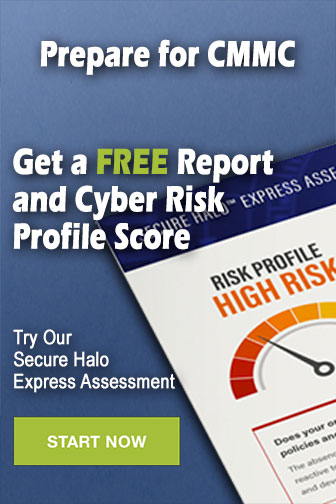