TM 1-1500-204-23-2
accordance with instructions contained in paragraph 4-5i (9).
(6)
Internal Inspection. Inspect hose assemblies internally for evidence of tube restriction due to collapse,
wire braid puncture, or other damage. Following methods for internal inspection are recommended.
(a)
Straight hose assemblies. Insert light at one end and inspect by looking through from the
opposite end.
(b)
Hose assembly with elbow fitting one end. Insert flexible inspection light into elbow fitting and
examine by looking through the opposite end.
(c)
Hose assemblies with elbow fitting both ends. Insert flexible inspection light into one end and
examine from the opposite end using a dental-type mirror. This procedure is only practical on large size hose
assemblies.
(7)
Disassembly. The hose can be completely disassembled using the following procedures (see figure 4-
45).
(a)
Place socket in vise and remove nipple assembly by applying wrench to nipple hex (see figure 4-
45, detail A).
(b)
Remove socket from vise and tap edge of pocket against flat surface to loosen pull socket back
onto hose to expose hose end and sleeve insert (see figure 4-45, detail B).
(c)
Remove sleeve inserting end of nipple into sleeve internal diameter and gently pry sleeve from
inner tube (see figure 4-45, detail C).
(d)
Remove socket by pulling or threading socket from hose.
(e)
Remove hose fitting on opposite end of assembly.
(f)
All removed hose will be condemned and disposed of in accordance with existing regulations.
(8)
Reusability Check. Use the following procedures to determine whether parts that are removed may be
reused.
(a)
Cleaning. Clean fittings in accordance with paragraph 4-5i (a).
(b)
Finishes. Examine all fitting details with anodized or plated finish for corrosion damage.
Condemn corrosion-damaged parts Minor scratches are not cause for replacement; however, parts with wrench, vise jaw,
or similar marks shall be replaced.
(c)
Flanges, sealing faces and/or swivel nuts Inspect these components as follows:
CAUTION
Use care when handling flange fittings to prevent damaging the gasket, flange or sealing face of pad or
fitting. Failure of equipment could result.
1
Check for wraping of the flange.
2
Check for damage to the sealing face of the flange fitting. Any damage, nicks, scratches,
etc., will be cause of rejection.
3
Check for multilated threads and evidence of overtightening (This will show up as a belled
condition or pulled condition or flared connections and may result in a frozen or tight swiveling nut).
4
Examine for backed-out retaining wires on wired-on swivel nuts. If backed-out wires are
found, drive wire back into nut using a drift pin of proper size and ball peen hammer.
(d)
Nipples. Visually inspect for sealing surface (chamfered area) for damage or galling on stainless
nipples (figure 4-46) and for the following defects:
1
Nicks, spiral or longitudinal scratches or scoring which could create an escape passage for
fluids.
2
Flare-out or distortion of cone seats resulting from over torquing.
3
Damaged or galled threads (nipple to socket thread) test by threading a new socket of
proper size on to the nipple threads.
4-57
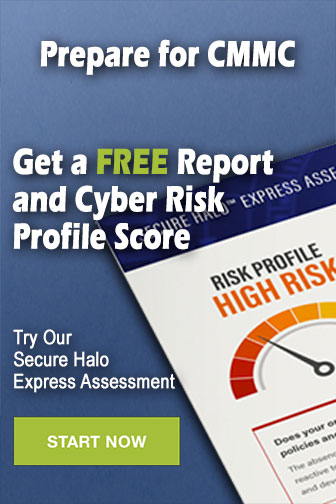