TM 1-1500-204-23-6
(e) A black residue at base of scratch where test was made indicates that scratch extends to core.
(f)
A white residue in base of scratch indicates that scratch does not extend through cladding.
NOTE
A second spot test in an unscratched area makes it easier to determine whether the
residue is black or white.
(5) Disposition. Only portions of sheet which are damaged beyond serviceability will be condemned. Use
serviceable portions of damaged sheets for manufacture of smaller parts and assemblies.
c.
Storage. Store aluminum alloys in a dry, fully enclosed area not exposed to weather or other corrosion inducing
conditions. Store sheet stock of clad and soft alloys on racks. Interleave the sheets with paper, Federal Specification
UU-P-553.
CAUTION
Do not store aluminum alloys near such sources of moisture as steam pipes or water
pipes. Damage to alloys may otherwise result.
Do not store in the proximity of such chemicals as caustics, nitrates, phosphates and
acids. Damage to alloys may otherwise result.
Do not store aluminum packed in original boxes in the open due to moisture
condensation. Damage to alloys may other- wise result.
Ensure that adequate protection is given to all aluminum alloys when transported.
Damage to alloys may otherwise result.
4-3.Magnesium Alloys . Light weight is probably the best known characteristic of magnesium. Aluminum is one and
one-half times heavier, Iron and steel are four times heavier, and copper and nickel alloys are five times heavier. Pure
magnesium has a specific gravity of only 1.74, and alloying does not increase the specific gravity to more than 1.83.
Magnesium is commonly alloyed with aluminum, manganese, and zinc to give it greater strength-to-weight
characteristics. Magnesium alloys can be cast and fabricated by practically every known method, and have excellent
machinability qualities. Also, they possess relatively high thermal and electrical conductivities and are nonmagnetic.
a.
Identification. Magnesium types are identified in table 4-7. Composition and marking identification are explained
in the following paragraphs.
(1) Composition Identification. Magnesium alloys are identified by their composition designation. The letters
indicate the principal alloying element; for example, AZ indicates that the main elements mixed with magnesium are
aluminum and zinc. Numbers which follow the letters indicate the percent of each of the principal alloying elements; for
example, AZ31 indicates that the alloy is composed of three percent aluminum and one-percent zinc.
(2) Marking identification. Magnesium alloys should be marked with a suitable marking fluid, such as ink,
Federal Specification TT-1-558.
(a) Plate and sheet. Use characters not less than 3/8 inch in height, in rows of recurring symbols from one
edge to the other, giving the following information:
Manufacturer's name or trademark.
Federal Specification QQ-M-44 and manufacturer's alloy number.
The thickness in inches and condition in which furnished.
(b) Rods, bars, and special shaped sections. Mark with the following information at 3-foot intervals along
the piece.
Manufacturer's name or trademark
The alloy number and Federal Specification QQ-M-31
The temper in which furnished.
4-14
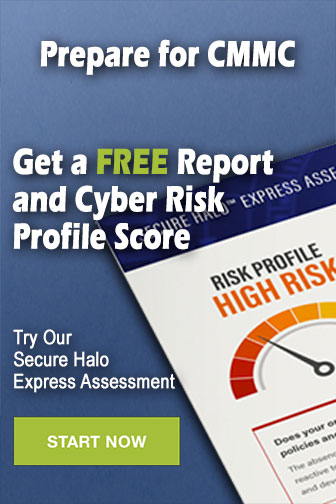