TM 1-1500-204-23-6
(3) Precautions. in case of fire use clean, dry sand, talcum powder, Federal Specification U-T-30, or clean, dry,
unrusted cast Iron chips to sprinkle a 1/2- inch deep layer over the area.
4-4.Steel Alloys. Alloy steels are produced by combining carbon steel with other elements to improve the properties of
steel. The most common of these alloying elements are silicon, manganese, nickel, vanadium, tungsten, molybdenum,
and chromium. Each of these elements gives some special property to the alloy in which it is used. Each element also
changes the rate and temperature at which the structure of the alloy changes during heat treatment.
a.
Identification. The composition of SAE steels is identified by a numerical index system. Each SAE number
consists of a group of digits which are defined as follows:
The first digit represents type of steel (refer to table 4-8); for example, 4150 indicates molybdenum steel.
The second digit represents percentage of principal alloying element; for example, 4150 indicates molybdenum
steel containing 1 percent molybdenum.
The remaining digits indicate percentage, in hundredths of 1 percent, of carbon in the alloy, for example, 4150
indicates molybdenum steel containing 1 percent molybdenum and 0.50 percent carbon.
NOTE
The percentages indicated in the SAE numbers are average; for example, the carbon
content of SAE 1050 steel may vary from 0.45 to 0.55 percent.
Table 4-8. SAE Numbers Used in Identification of Steels
Type steel
Classification
Carbon
1000 Series
Nickel
2000 Series
Nickel-Chromium
3000 Series
Molybdenum
4000 Series
Chromium
5000 Series
Chromium-Vanadium
6000 Series
Tungsten
7000 Series
Silicon-Manganese
9000 Series
b.
Marking..
When steel is received from the mill it should have the following markings: manufacturer's name or
trademark, specification number, class, composition, condition, grade or type, and nominal thickness. Sheet and plate
steel strips will be tagged. If it has not been marked by the mill, mark as follows:
WARNING
Drycleaning solvent is flammable and solvent vapors are toxic. Use P-D-680, Type II
Solvent in a well-ventilated area. Keep away from open flames. Avoid prolonged
solvent contact with skin.
(1) Clean all grease, dirt, and foreign matter from surface to be painted using drycleaning solvent, Federal
Specification P-D-680.
(2) Paint each item with parallel stripes of equal width, 1/2 to 3/4 inch wide, placed side by side and in sequence
so that when read from nearest end of bar toward middle, the material designation is shown (see figure 4-1). Colors of
each band must be in accordance with table 4-9. The markings will be painted in stripes on each tube, bar, rod, sheet, or
plate using enamel, MIL-E-7729.
4-17
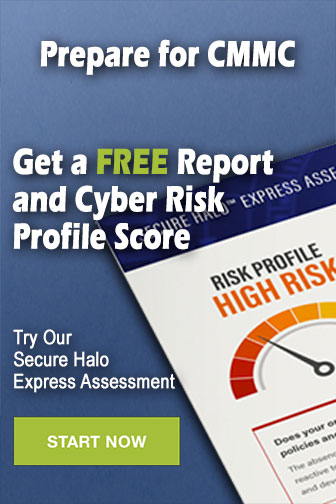