TM 1-1500-204-23-6
(3) Leave a space between stripes of not more than 1/4 inch, when two or more like colors appear adjacent to
each other.
(4) Leave a space of 3/4 to 1 inch between stripes representing first two digits and last two digits of steel
designation.
NOTE
Steel identification is shown in table 4- 10.
Steels that require marking, but cannot be identified and marked, should not be used
for repair of aircraft
Color marking does not apply to corrosion-resistant steels, low carbon alloy steel, or
tool steels.
4-5.Titanium and Titanium Alloys . Titanium is a light, strong, corrosion-resistant, ductile metal, situated between the
aluminum alloys and corrosion-resistant steels insofar as modulus, density, and strength at intermediate temperatures
are concerned. At normal temperatures, commercially pure titanium and titanium alloys have excellent corrosion
resistance to sea water and marine atmospheres. Titanium and titanium alloys are used chiefly for parts which require
good corrosion resistance, moderate strength, light weight, and oxidation resistance at temperatures up to 1200 °F
(6490°C). Machinability of titanium and its alloys is poor. If titanium is not available for a repair, substitute material
should be 4130, 4140, 4340, or 8630 steel of same gauge.
NOTE
Due to its cost, titanium is used only where outstanding advantages will be realized.
a.
Forming. Commercially pure titanium is formed at temperatures from 400 to 600 °F (204 to 316°C), where large
deformations are necessary.
(1) Form commercially pure titanium by hydropress, stretch press, brake roll forming, drop hammer, and other
similar operations. It is more difficult to form than annealed corrosion-resistant steel.
NOTE
The alloy sheet can be formed to limited extent at room temperature
Severe deformation occurs at elevated temperatures up to 1500 °F (816°C).
(2) Form in annealed condition if strength of finished part is acceptable without subsequent heat treatment.
NOTE
Quenching introduces serious distortion.
(3) Stress relieving is required after forming.
(4) Use monel rivets or standard close tolerance steel fasteners for installation of titanium parts.
b.
Inspection. Titanium is nonmagnetic and the penetrant type inspection will be required.
c.
Identification. Titanium and titanium alloys are identified by class in table 4-11. Titanium alloys can be identified
by composition designation. Titanium alloy, 6AL-4V, has the following nominal chemical composition of six percent
aluminum, four percent vanadium, and the balance is titanium.
d.
Marking. Mark titanium alloys with a suitable marking fluid, such as ink, Federal Specification TT-I-558.
(1) Sheet and strip. Use characters not less than 3/8 inch in height, in rows of recurring symbols at intervals not
greater than 3 feet throughout the length, giving the following information:
Manufacturer's name or trademark.
Composition or commercial alloy number.
4-18
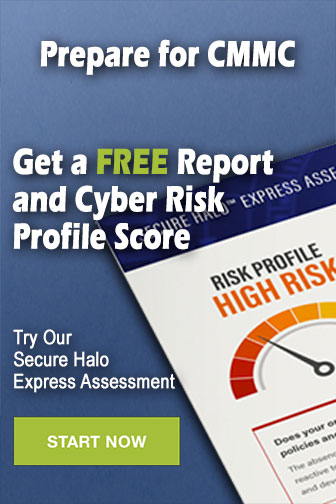