TM 55-4920-328-13
horsepower, torque, temperature, vibration, oil pressure
and quantity, and water brake temperature and
pressure. Refer to paragraph 1-5 for leading particulars
of the test trailer assembly.
(1) Test Trailer Module.
(a) The test trailer module (figure 1-3)
consists of a frame and running gear assembly (3),
crane assembly (10), 2 slave units (12), 4 latch arm
guide assemblies (17 through 21), storage box (8), cable
trays (14), deck plates (13), forward and aft leveling
jacks (11), torque arm assembly (16), and associated
plumbing and cabling. The unit also mounts the
hydraulic start system (4), electric start system (5), fuel
system (1), oil system (6), air system (2), and the
portable oil lubricating unit pumping assembly (7). One
slave unit actuates the engine fuel control overspeed
governor (Nil) lever during engine test. The other slave
unit actuates the engine fuel control (NI) power during
engine test. The two slave units are remotely controlled
by master control units in the control cab module. The
four latch arm guide assemblies provide a means of
supporting and stabilizing the engine dolly assembly
during engine testing. After the dolly axle is lowered to
the latch arm guide assembly, the latch arm (20) is
positioned over the axle. The swing eye bolt with
handle (21) fits into the end slot of the latch arm. The
latch arm is secured by turning the handle in a clockwise
direction.
NOTE
U. S. Army (USATSARCOM) authorized
ECP No. MEG-01, dated March 26, 1981,
identifies the replacing of the gasoline
engine driven hydraulic starting unit and
the battery starting system with a Christie
Rectifier Power Supply starting system.
(Army supported electrically driven units
are currently available. )
(b) The storage box is located on the test
trailer deck in front of the hydraulic and electric start
systems. The storage box is 44. 00 inches long, 14. 00
inches wide, and 14. 00 inches high and is bolted to the
test trailer deck. The storage box is used for storing
torque arm weights. Two cable trays which provide
support for 4 hose assemblies and 7 cable assemblies
are located beneath the right side of the test trailer deck.
The aft cable tray is approximately 59. 12 inches long,
20. 06 inches wide, and 5. 56 inches deep. The
forward unit is approximately 35. 00 inches long, 20.
06
inches
wide and 5. 62 inches deep. A third cable storage tray
is located beneath the forward test trailer deck. The
storage tray is 40. 25 inches long, 33. 75 inches wide,
and 6. 50 inches deep. The aft deck plate is 95. 12
inches wide, 60. 37 inches long, and 0. 25 inch thick.
The forward deck plate is 95. 12 inches wide, 65. 12
inches long, and 0. 25 inch thick. The two deck plates
are formed of diamond tread aluminum plate.
Significant details of the equipment installed on the test
trailer module are described in subsequent paragraphs
in this section.
(2) Test trailer frame and running gear assembly.
The test trailer frame and running gear assembly (figure
1-4) consists essentially of a frame assembly (2),
running gear and brake system assembly (6), dolly
support frame (1), 3 stop lights (4,5) and 2 signal lights
(3). The aft running gear has dual 15-inch wheels with
pneumatic tires. The forward running gear has a
steerable axle assembly with a removable drawbar (8)
and two 15-inch wheels with penumatic tires. The
brakes are air/ hydraulic. The aft parking brake is
manually controlled by operating a brake lever (7) on
the right side of the test trailer. The dolly support frame
is a welded assembly 66. 00 inches long, 96. 00 inches
wide, and 8. 00 inches high and is bolted to the frame
of the test trailer assembly.
(3) Crane assembly. The hydraulically-operated
crane assembly (figure 1-5) is used to lift an engine test
dolly assembly (figure 1-28), with engine mounted, from
the ground to the test trailer deck for engine testing.
The crane assembly is mounted on the left forward
corner of the test trailer deck. The crane assembly
consists essentially of a mast assembly (4, figure 1-5),
boom assembly (3), boom assembly (3), boom
extension (2), hydraulic hand pump (5), and a piston and
cylinder assembly (9). Additional components of the
crane assembly consist of a brake assembly (8), pump
handle (6), well assembly (7), and a chain and hook
assembly (1). The lifting capacity of the crane assembly
varies with the position of the boom extension. With the
boom extension fully extended, the lifting capacity is
limited to 1,100 pounds. With the boom extension fully
retracted, the maximum lifting capability is 4,000
pounds. The maximum boom swing is 210 degrees.
The brake assembly is used to restrict or prevent crane
rotation, when required. The manual release valve (10)
is used during operation. Instructions for operation of
the crane assembly are provided in chapter 2 of this
technical manual.
1-4
Change 4
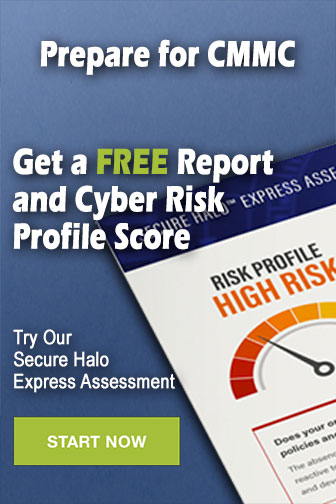