TM 55-4920-328-13
CB1 Air System
CB2 Fuel System
CB3 Oil System
CB4 Beacon Light
CB5 Instrument Power Supply
CB6 Portable Oil Unit
CB7 Spot Lights and Blowers
CB8 Instrument Power
CB9 Utility Outlet and Overhead Lights
CB10 Heat Pump
CB11 Motor Starter Control
CB12 Oil Pre-Heat Subsystem
CB13 Trickle Charger
(d) Control cab module.
1. The control cab module (1, figure 1-21)
contained
in
the
control
cab
assembly
consists
essentially of an enclosure which houses METS controls
and instrumentation. The control cab module is
equipped externally with a 360-degree rotation, 200-watt
flashing red beacon light (2) which operates during a
test. Two spot light assemblies (3) are mounted on the
forward wall of the control cab module to provide
illumination during a test, when required. The interior of
the control cab module contains three overhead
fluorescent light fixtures, electric starter motor starting
controls, hydraulic starter motor starting controls,
generator control and fault indicator panels, and a circuit
breaker panel assembly (25), containing the main circuit
breaker and 13 facility circuit breakers. A heat pump (8)
is mounted in the upper left aft wall of the control cab
module for environmental control. An asbestos/rubber
floor matting is installed on the floor of the unit.
Electrical ducts for internal wiring and cable assembly
protection are provided in the control cab module.
Thirty cable assemblies (exclusive of the cable
assemblies contained in the four consoles) are provided
with
the
control
cab
module
for
electrical
interconnection. External electrical connections to the
control cab module are made at the control cab rear
connector plate, the main power interface plate, and the
test trailer bulkhead box assembly (11, figure 1-21). A
ground rod (9) is stowed above the floor of the cab
along the bottom of the four instrumentation sub-
modules, when not in use for electrical grounding
protection during operation of the system. Fan-type
blowers are provided in the left and right hand castle
assemblies (Units 8 and 9) (14,16) to provide through
circulation of air for instrumentation cooling. A forward
writing surface assembly (12), 16 inches deep, extends
the width of the control cab module above the lower
sections of the four instrumentation sub-modules. A
rear writing surface assembly (26) extends the width of
the control cab module forward of the aft wall of the
enclosure.
2. Control cab. The sound-attenuated control cab
module (1, figure 1-21) is approximately 92 inches long
and 96 inches wide with an internal height of 77.50
inches. The control cab module is equipped with a
hinged door 30 inches wide and 72 inches high. The
door opens through an arc of 110 degrees to a detent,
and will continue opening through a total arc of 165
degrees where the door may be latched in the full-open
position. A bullet-proof plate glass window, 2.00 inches
thick, 15.50 inches high, and 41.50 inches wide is
located in the forward wall of the control cab. The wall
containing the window is constructed of 3/U-inch steel
for operator protection.
3. Heat pump. The heat pump (8, figure 1-21) is
installed in the left rear wall of the control cab module.
The heat pump operates in the same manner as a
conventional room-type cooling and heating unit. The
heat pump has high and low speed control for both
cooling and heating, separate ventilation and exhaust
systems, and an automatic thermostat to provide
protection at temperatures below 32 °F. The unit is also
equipped with front and side airflow control and is
mounted on a slide-out chassis for servicing and
removal or installation. The unit operates on 208v ac,
60 Hz single-phase current from a receptacle on the rear
wall of the control cab.
(e) Diagnostic sub-module (unit 1). The
diagnostic sub-module (figure 1-22) consists essentially
of a modular cabinet assembly which contains the
instrumentation used to monitor engine parameters
during a test. Digital display of discrete parameters is
made on the panel mounted instrumentation listed
below. The cabinet assembly provides mounting for 29
cable assemblies and a bottom connector mounting
panel assembly, 2 signal distribution terminal board
assemblies,
a
power
distribution
terminal
board
assembly, 4 lacing bars, and 2 lacing bar assemblies.
Three upper and lower, left and right rear support
brackets are installed on the aft frame of the cabinet
assembly to accommodate the chassis track slides of
removal rack-mounted components. Instrumentation
contained in the cabinet assembly, and shown in figure
1-22, includes the following:
Temperature
and
Torque/Pressure
Digital
Indicator 1A1 (1,4)
Data Selector Assembly 1A2 (7)
Vertical Tape Indicator Assembly 1A3 (9)
Thermocouple J unction 1 AD (11)
Data Multiplexer 1A5 (14)
1-26
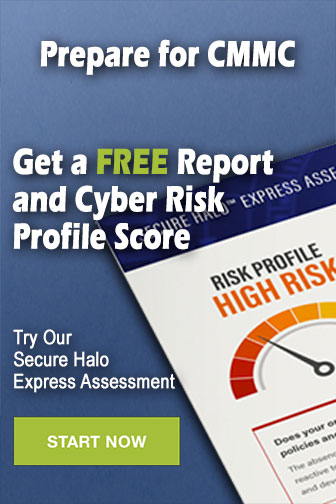