TM 55-4920-328-13
3. Multi-channel vibration meter 2A3. The
multi-channel vibration meter (21, figure 123) is a
standard-width, rack-mounted unit that mounts four
vibration meters. The multi-channel vibration meter
consists essentially of a 19-inch chassis assembly that
simultaneously monitors four vibration channels. The
vibration input signals are displayed on four identical
meters. Output of each channel may also be displayed
on an external meter or oscilloscope. Plug-in filters are
used in each channel to eliminate all unwanted
frequencies outside the range of the frequencies being
monitored. An on-off switch is located on the rear panel
of the unit. The unit consists of four identical sections,
each consisting of a vibration meter (22), FILTER
SELECT control (23), RANGE control (24), MODE control
(25), CAL adjustment potentiometer (26), SCOPE jack
(27), channel selector INPUT switch (28), FILTER jack
(29), and SENS adjustment potentiometer (30). When
connected to vibration pickups mounted on the engine
under test and the power switch is ON, the FILTER
SELECT control is placed to the appropriate position to
select the desired filter for signal conditioning and the
RANGE control is then adjusted so that the meter displays
readings at or above the mid-range position on the meter.
If peak-to-peak displacement readings are desired, the
appropriate channel MODE control (25) is set to D to
display displacement in mils. If average velocity readings
are desired, the MODE control is set to V to display
velocity in interruptions per second. The multi-channel
vibration meter is used in conjunction with external charge
amplifiers and filters (21A, figure 1-21) to extend its
operational range for certain external accelerometers.
Adjustment procedures are included in Chapter 2 with
applicable engine test preparations.
4. Fuel flow/Oil consumption signal
conditioner panel assembly 2A9. The fuel flow/oil
consumption signal conditioner panel assembly (31, figure
1-23) is a rack-mounted unit that provides a mounting
enclosure for a fuel flow signal conditioner 2A9A1 and a
frequency converter 2A9A2. The unit consists essentially
of a signal conditioner chassis assembly 19.00 inches
wide, 5.22 inches high, and 8.63 inches deep, exclusive
of the left and right track slides. The front panel is
provided with left and right handles and knurled retaining
screws to secure the unit in the engine analyzer sub-
module. Terminal board assembly TB1 is installed on the
bottom panel of the chassis assembly. Four connectors
J1, J2, J3, and J4, are mounted on the rear panel of the
chassis assembly.
a. Frequency converter 2A9A2. The frequency
converter (58, figure 7-16) is a unit used in the oil
consumption signal conditioner circuitry to convert input
voltages from 0 to 10 mv dc from 2A10 to output
frequencies ranging from 0 to 10k Hz. Two adjustments,
ZERO and RANGE, are provided on one end of the unit.
b. Fuel flow signal conditioner 2A9A1. The fuel
flow
signal
conditioner
(62,
figure
7-16)
is
an
encapsulated unit used to condition signals from a
flowmeter installed in the fuel system. The fuel flow
signal conditioner is installed in the fuel flow/oil
consumption signal conditioner panel assembly 2A9. The
signal conditioner accepts pulsating signals from the
flowmeter at frequencies from 5 to 2,000 Hz and amplifies
these signals to provide an output signal to the monitor
unit. The signal conditioner consists of a carrier pickup
module, a regulated power supply, a 0.5ampere fuse, a
stepdown transformer and full wave bridge rectifier, and a
5k ohm attenuation potentiometer. Excitation voltage at
117v ac, 60 Hz is applied to the transformer and rectified
to 10v dc at 50ma. This voltage is applied through a filter
network in parallel with a 10-volt Zenar diode. The
nominal 10-volt output is applied to the carrier pickup
module which utilized oscillator, modulator, demodulator,
amplifier, and shaper circuits. Output of the module is the
input to the digital frequency indicator and, through the
frequency converter PC5-1A3 (D to A). For the vertical
tape indicator (1A3), to provide display of fuel flow of the
engine under test in pounds per hour. The attenuator
potentiometer may' be adjusted to suit the sensitivity
requirements of the digital indicator unit which is pre-set
to the corresponding K-Factor correction.
5. Oil quantity electronic unit 2A10. The oil
quantity electronic unit (32, figure 1-23) is a standard-
width, rach-mounted readout unit contained in the engine
analyzer
sub-module
assembly
to
provide
visual
indication of oil mass consumption, engine internal oil
integrity, and oil leakage, when connected to an external
probe. The unit is 19 inches wide, 5.22 inches high, and
12.25 inches deep, exclusive of the left and right slides.
Left and right handles and knurled fasteners are installed
on the front panel. Three OIL PROBE potentiometers:
ZERO, DRY, and FULL, are mounted on the front panel.
An on-off switch (39), indicator light (40), and a 1-ampere
3AG fuse (38) and fuseholder are installed on the front
panel on the lower left side. Connectors J1 and J2 are
mounted on the rear panel adjacent to eight
Change 2 1-39
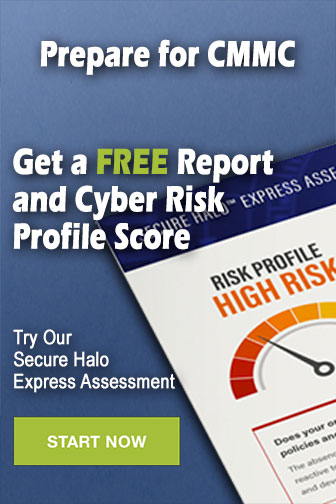