TM 55-4920-328-13
1. Operator's panel assembly 3A1. The
operator's panel assembly (1, figure 1-24) -is installed in
the uppermost position of the sloping front section of the
cabinet assembly. The operator's panel assembly
consists of a standard rackmounted chassis assembly 19
inches wide, 4.34 inches high and approximately 13
inches deep, excluding the length of the slide track
assemblies. The chassis assembly is provided with left
and right handles and lock release pins which may be
disengaged to allow the chassis assembly to be tilted
downward to upward to facilitate maintenance of the unit.
The front panel is equipped with four openings. The two
left cutouts on the front panel are used for mounting a
TORQUE PRESSURE indicator M1 (2) and an IGV
ACTUATOR ARM indicator M2 (3). The two right
openings are covered with sheet metal cover plates to
exclude foreign matter from the interior of the unit.
Terminal boards TB1, TB2, and TB3 are installed in the
chassis assembly to route and terminate the internal
cabling wire runs. Two connectors, J1 and J2, are
installed on the external side of the rear panel for
interconnection of the unit with other components of the
system. The two blank panels are removed, when
required, for installation of instrumentation contained in
certain engine accessories. A rectangular hole pattern is
located in the lower left portion of the chassis assembly
for mounting an inverter, also contained in an engine
accessories. Refer to chapter 2 of this manual for further
information on these components.
a. Torque pressure indicator M1. The TORQUE
PRESSURE indicator (2, figure 1-24) is a single-needle
Autosyn type indicator used to display pressures
transmitted from the torque system through a pressure
transmitter. The indicator is graduated from 0 to 200 psig
in 2-psi increments. Excitation for the indicator is
provided by system 26v ac, 400 Hz power. The indicator
is supplied input signals from the pressure transmitter MT-
5. The two instruments comprise a functional sub-loop.
Movement of the indicator rotor is controlled by the
strength of the magnetic field within the associated stator
windings induced by input analog signals. Rotation of the
needle and rotor shaft is directly proportional to the input
signal level supplied from the pressure transmitter.
b. IGV Acutator arm indicator M2. The IGV
ACTUATOR ARM indicator (3, figure 124) is an
instrument that provides display of relative positions of
the engine inlet guide vane actuator arm during a test.
26v ac, 400 Hz excitation power is input to the instrument
at connector pins A and B. Analog signals from a remote
IGV actuator arm position transmitter connected to the
data acquisition assembly are input to the indicator.
Needle movement to display inlet guide vane actuator
arm position is provided by a Magnesyn type assembly
contained in the indicator case. Movement of the
indicator rotor is influenced by the strength of the
magnetic field induced within the associated stator
windings. The rotation of the needle and rotor shaft is
directly proportional to the input signal value from the
transmitter.
2. Operator's panel assembly 3A2. The
operator's panel assembly (7, figure 1-24) is located in the
upper portion of Unit 3 below the operator's panel
assembly 3A1. This unit is similar to the panel assembly
located immediately above. The panel assembly consists
of a rack-mounted chassis assembly 19 inches wide, 4.34
inches high, and 12.75 inches deep, excluding the length
of the track slide assemblies. Left and right handles and
lock release pins are installed on the front panel of the
chassis assembly. The front panel also mounts an
EXHAUST
GAS
TEMP
meter
M1
(38),
a
GAS
PRODUCER meter M2 (4), a POWER TURBINE meter
M3 (5), and an OIL TEMP meter M4 (6). Terminal boards
TB1 and TB2 are installed within the chassis assembly to
route and terminate the internal cabling wire runs. Three
connectors J1, J2, and J3, are installed on the external
face of the rear panel to facilitate interconnection of the
operator's panel assembly with other units in the system.
a. Exhaust gas temp meter M1. The EXHAUST
GAS TEMP meter (38, figure 1-24) is a solid state,
combination pointer, indicating and digital counter type of
instrument used to display exhaust temperatures of an
engine during a test. The indicator senses an input signal
from a chromel-alumel thermocouple junction. The signal
is applied to a cold junction compensation unit which
compensates for ambient temperature changes within the
instrument. The compensator forms one leg of a bridge.
Output of the compensator is connected through a filter,
which rejects spurious ac line frequencies, to a chopper.
The other leg of the bridge incorporates a slidewire
potentiometer. The chopper alternately applies the
compensated signal and the potentiometer signal to a
servo amplifier. Unbalance between input signals to the
amplifier results in a generated signal which drives a
servo mechanism. The
1-43
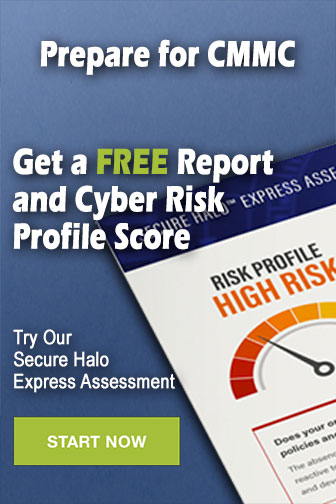