TM 1-1500-204-23-1
CAUTION
Use only dehydrated air with a
maximum relative humidity of 30
percent for pressurizing shipping
containers in order to keep humidity
as low as possible in the air
surrounding the engine.
(c) Pressurize container to 5 psi with dehydrated
air.
(d) Retighten engine container flange nuts to
original torque after 1 hour elapsed time.
(e) After container has been pressurized, use
soapy water to check for leaks If a second pressure
check in 24 hours does not Indicate a leak, engine is
ready for storage or shipment.
(f) Maintain all markings and stencils on shipping
container intact without additions or deletions.
c. Preservation of Inoperable Engines. Engines that
cannot be operated and are to be removed from aircraft
shall be treated as far as practicable as shown in
paragraph 7-11 b. Spray all possible interior surfaces,
as the engine will be shipped or stored without the
protection afforded It by a final operation using a
corrosion-preventive
compound
in
the
lubrication
system. An appropriate entry shall be made on DA
Form 2408-16 and DD Form 1577-2, stating Inability to
accomplish preservation run of the engine DA Form
2408-5 also will be sent with the, engine, if applicable
DA Form 2410 will be completed and mailed in
accordance with DA PAM 738-751.
d. Intermediate Storage of Engines Mounted on
Aircraft. Intermediate storage shall be completed within
24 hours after ground runup. When it is not definitely
known that the aircraft will be operated within 45 days,
the engine shall be preserved for intermediate storage
and an entry shall be made on the applicable DA Form
2408 series stating this work has been accomplished.
The procedure for Intermediate storage is the same as
previously outlined in paragraph 7-11b with the following
additional procedures.
(1) Drain fuel from engine-driven fuel pump and
flush interior with lubricating oil, MIL-L-6081, grade
1010, while rotating engine crank-shaft. Seal fuel lines
with suitable plugs.
CAUTION
Use dehydrated air with a relative
humidity
of
30
percent
for
all
spraying operations. Damage may
otherwise result.
(2) Spray exhaust valves with corrosion preventive,
MIL-C-6529, Type II Spraying shall be through exhaust
port with exhaust valves fully open.
NOTE
Engines with collector rings may be
sprayed through spark plug ports
with exhaust valves fully open.
(3) Place and secure two 8-unit bags of desiccant,
Military Specification MIL-D-3464, in carburetor air
intake scoop or carburetor adapter.
(4) Cover open end of scoop with a suitable
anchored, barrier paper, MIL-B-131.
(5) Firmly attach a red cloth streamer to bags
containing desiccant and bring loose end out In such a
manner that not less than 18 inches of cloth streamer
will be visible on outside of carburetor air Intake scoop.
In order to prevent streamer from action as a wick, a 3-
to 4-inch length of lockwire shall be left between
streamer and desiccant.
(6) Install 16 units of desiccant, MIL-D-3464, in
exhaust outlet on engines incorporating an exhaust
collector ring. Place a total of four units of desiccant in
exhaust openings on engines that do not have an
exhaust collector ring.
(7) Firmly attach a red cloth streamer to bags
containing desiccant and bring loose end out a minimum
of 18 inches. Use a 3- to 4-inch length of lockwire
between cloth and desiccant to prevent streamer from
acting as a wick.
(8) Seal all openings, joints, drain holes, and outlets
with barrier material, MIL-B-1 21, and secure with
pressure sensitive tape, Federal Specification PPP-T-
60.
7-43
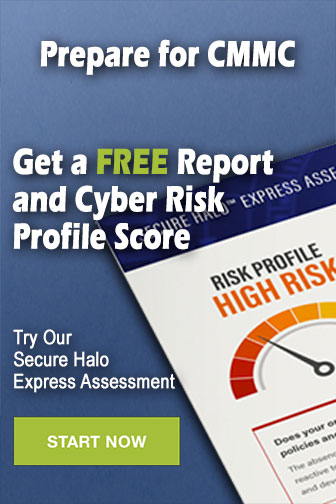