TM 1-1500-204-23-1
CHAPTER 8
GENERAL TURBINE ENGINE MAINTENANCE
8-1. General. The maintenance Instructions and
procedures contained in this chapter are general and
applicable to turbine engines used on Army aircraft
Maintenance Instructions that are specific and peculiar
to particular engines are contained In the applicable
maintenance manuals and will be used in conjunction
with general information contained in this chapter.
8-2. Engine Types and Designations. Turbine engine
types and designations are explained in the following
paragraphs.
a. Types. Types of aircraft turbine engines are the
centrifugal-flow
and
axial-flow
turbine
engines.
Centrifugal-flow engines, as shown In figure 8-1,
compress the air by centrifugal force. The air enters the
air inlet and is directed to the compressor inducer vanes
through circumferential inlets located in front and back
of the Impeller. Axial-flow engines, as shown in figure
8-2, compress the air axially. The air enters the air inlet
and flows in a relatively straight path In line with the axis
of the engine.
b. Designation Examples. On gas turbine engine
designations, such as T53-L-1, T denotes gas turbine
with drive shaft, numeral 53 is assigned to the engine by
the services, L denotes the manufacturer, and 1 denotes
major modification.
8-3. Turbine Engine Theory. The gas turbine engine
is a type of internal combustion engine that produces
power by a continuous and self-sustaining process of
compression, combustion, expansion, and exhaust. Air
is compressed in the compressor section, mixed with
atomized fuel and burned in the combustion chambers.
As the fuel burns, the resultant gases expand through
turbine wheels to convert heat energy to useful power
8-4. Turbine Engine Precautions. The following
precautions shall be observed during maintenance of
turbine engines.
a. Regularly police parking areas, runways,
taxiiways, and runup and exhaust areas to ensure
against the presence of foreign objects which could
enter the engine. Special attention shall be given to
cleaning of cracks and expansion seams in hard
surfaced areas where engines will be operated, as tests
have indicated that these are the main source of foreign
objects which are ingested.
b Periodically instruct personnel concerned with
aircraft maintenance of foreign object hazards to ensure
that maximum preventive measures are taken.
c Ensure that air inlet and tailpipe dust excluders are
installed at all times when engines are not being
operated, except when it is known the engine will again
be operated Immediately following shutdown.
d. Prior to each engine start, thoroughly Inspect and
clean inlet ducting. Remove all loose nuts, bolts, tools,
or other objects which would cause engine damage and
possible subsequent failure.
e. After work has been accomplished, inspect to
ensure that all accessories and attaching parts are
secure and that work areas are cleared of foreign
objects prior to engine operation.
f. Provide properly marked receptacles (FOD cans) in
all work areas into which trash, ferrous and nonferrous
scrap, safety wire, etc. , may be placed.
g. Adhere to applicable gas turbine-powered aircraft
taxiing and parking procedures as outlined in applicable
technical bulletins. This minimizes damage due to
objects being thrown by the exhaust blast Into the intake
of other aircraft.
h Ensure that gas turbine-powered aircraft takeoff
and landing procedures are such as to avoid the intake
of foreign objects blasted from runways and runway
shoulders by preceding aircraft.
i. Use inlet duct runup screens during all ground
operations, including taxiing to and from takeoff
position, with the following exceptions:
·
Inlet duct runup screens are not required on
aircraft using centrifugal flow engines.
Change 3 8-1
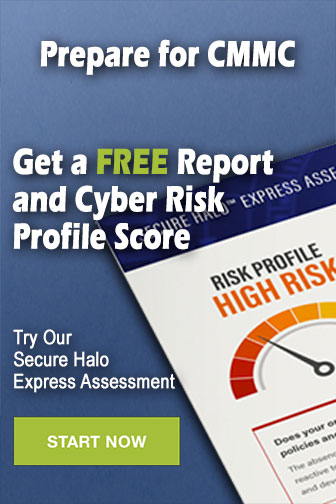