TM 1-1500-204-23-1
(2)
Inspect lining recesses in piston,
center carrier, and anvil for indications of wear which
could cause loss of lining. Wear of anvil lining recess
circumference in excess of 0.005 inch is cause for
replacement.
(3)
Examine piston cavity for corrosion,
excessive wear, or for being out-of-round. When light
corrosion extends more than 9/16 inch into piston cavity,
or heavy corrosion Is evident, replace brake assembly.
NOTE
Corrosion is usually found in carrier
housing and in piston cavities.
Corrosion in magnesium can be
Identified
by
the
rough
honeycombed appearance of the pit.
Pits are usually filled with a yellow or
gray powder. Heavy corrosion is
defined as pits that exceed 0.025
inch in diameter or grouped with
three or more pits of any diameter in
an area of 1/4 Inch square.
e.
Corrosion Treatment of Brake Assemblies.
Brake assemblies are manufactured from magnesium,
aluminum, and steel Most assemblies have magnesium
housings which are very susceptible to corrosion,
especially in piston cavities. Treat the surface using the
following procedures.
(1)
Remove sharp edges of corrosion pits
with crocus cloth, Federal Specification P-C-458,
lubricated with hydraulic fluid, MIL-H-5606.
(2)
Rework minor dents, nicks, burrs, or
gouges to break all sharp edges of indentations which
might result in a concentration of stress. Use a smooth
cut hand file to accomplish this, followed by fine
abrasive paper, Federal Specification P-P-101, to
remove tool marks.
(3)
Condemn brake assemblies that have
deep scratches, gouges, or cracks exceeding limits
established In applicable aircraft maintenance manual.
(4)
Accomplish
surface
treatment
as
outlined in TM 43-0105.
f.
Repair and Replacement of Brake Assembly
Components. Repair or replace brake assembly
components
in
accordance
with
the
applicable
maintenance
manual
and
the
following
general
procedures:
CAUTION
Care must be used when installing
seals and cups to prevent damage to
feathered edges.
(1)
Replace all seals, cups, and O-rings
on an availability basis when assembling brakes to
prevent possible leakage and brake failure.
(2)
Apply a light coat of insulating and
sealing compound, MIL-I-8660, to surface of piston
cavity and to O-ring or cup seal.
(3)
Replace
disks
that
have
cracks
extending through disc. Any single crack that extends
through thickness of brake disk shall be reason for
replacement. Minor surface cracks and heat checks are
normal and are not cause for replacement.
(4)
When necessary to replace one lining
because of wear, all linings shall be replaced. Replace
linings when any lining thickness is less than 1/16 inch,
or shows indications of being overheated.
g.
Brake Assembly Servicing. Service brake
assemblies
in
accordance
with
the
applicable
maintenance manual. The following are general
procedures for all aircraft.
(1)
Check for leaks while system Is under
operating pressure.
NOTE
Tighten
loose
fittings
with
the
pressure off.
(2)
Check all flexible hoses carefully for
swelling, cracking, or soft spots, and replace if evidence
of deterioration is noted.
(3)
Maintain the proper fluid level at all
times to prevent brake failure or the introduction of air
into the system.
h.
Bleeding Brakes. Air in the system is
indicated by a spongy action of the brake pedals. If air
is present in the system, remove it by bleeding the
system. There are two general methods of bleeding
brake system. Bleeding from the top downward (gravity
method) and bleeding from the bottom upward (pressure
method). Each method is explained in the following
paragraphs.
9-9
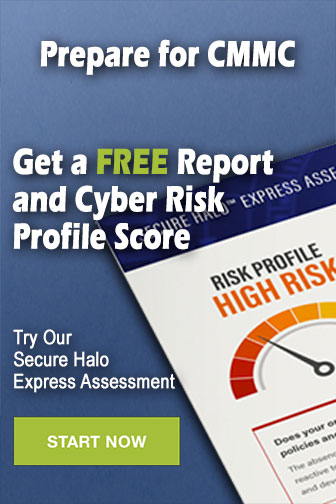