TM 1-1500-204-23-1
Immediately after landing, as ice will form on tube when
aircraft is left standing without tube being cleaned of
water, mud and slush.
(b) Maintain proper air-oil levels in struts as
specified on data plates. Use hydraulic fluid, MIL-
H5606.
(c) Replace
pistons
having
nicks,
scratches, or dents deep enough to cause leakage.
Replace elongated bushings. Replace struts that have
cracked fittings.
(d) When overhauling a pneumatic shock
strut, all ferrous metal parts will be magnetic particle
Inspected for cracks and flaws. Inspection will be
accomplished
in
accordance
with
applicable
maintenance manual.
(2) Rubber block type.
Replacement
of
compression and rebound rubber blocks, or adjustment
of preload tubes shall be as specified in applicable
aircraft maintenance manual
(3) Spring steel type. Repairs are limited to
burnishing minor nicks, burrs, or scratches Replace
cracked struts.
9-6. Landing Gear Alignment. The alignment of
aircraft landing gear is too critical, and the tolerances
too narrow to deal with the subject in a general manner.
Reference
will
be
made
to
applicable
aircraft
maintenance manual for specific data relating to landing
gear alignment.
9-7. Brake Systems. Brake system types and general
maintenance are explained In the following paragraphs.
a.
Brake Types. The three types of brake systems
in general use are the independent, power control, and
power boost systems. Each is explained in the following
paragraphs.
(1) Independent systems. In general, the
independent brake system is used on small aircraft.
This type of brake system is termed independent
because it has its own reservoir and is entirely
independent of the aircraft main hydraulic system.
Independent brake systems are powered by master
cylinders similar to those used in the conventional
automobile brake system. The system is composed of a
reservoir, one or two master cylinders, mechanical
linkage which connects each master cylinder with its
corresponding brake pedal, connecting fluid lines, and a
brake assembly in each main landing gear wheel as
shown in figure 9-7.
(2) Power control systems. Power brake
control valve systems, as shown in figure 9-8, are used
on aircraft requiring a large volume of fluid to operate
the brakes. As a general rule, this applies to many large
aircraft. Because of their weight and size, large wheels
and brakes are required. Larger brakes mean greater
fluid displacement and higher pressures, and for this
reason independent master cylinder systems are not
practical on heavy aircraft. In this system a line is
tapped off from the main hydraulic system pressure line.
(3) Power boost systems. A typical power
boost brake system, as shown in figure 9-9, consists of a
reservoir, two power boost master cylinders, two shuttle
valves, and the brake assembly in each main landing
wheel. In this type of system, a line is tapped off the
main hydraulic system pressure line, but main hydraulic
system pressure does not enter the brakes. Main
system pressure is used only to assist the pedals
through the use of power boost master cylinders.
b.
Brake
Assemblies.
Brake
assemblies
commonly used on aircraft are the single-disk, dual-disk.
The single and dual-disk types are more commonly used
on small aircraft.
(1) Single-disk brakes. With the single-disk
brake, braking is accomplished by applying friction to
both sides of a rotating disk which is keyed to the
landing gear wheel. There are several variations of the
single-disk brake, however, all operate on the same
principle and differ mainly In the number of cylinders
and the type
Figure 9-7. Independent Brake System
9-7
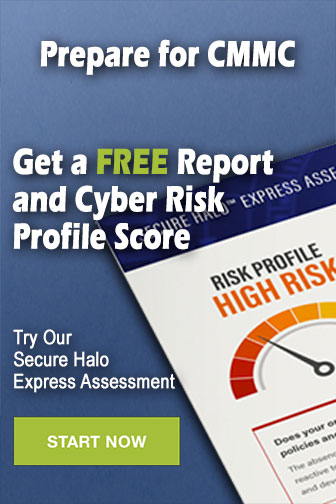