TM 1-1500-204-23-1
NOTE
·
Aircrew members who perform flight
duties away from home station or
assigned
unit
will
ensure
that
Individual
emergency
type
parachutes
and
harnesses
are
inspected every 30 days by qualified
parachute inspectors. However, if a
situation occurs which precludes
inspection due to a lack of qualified
parachute
inspection,
personnel,
parachutes
and
harnesses
may
continue to be used until arrival at a
facility
which
can
satisfy
the
inspection
criteria,
as
soon
as
practical. In no case will the 30 day
inspection requirement exceed 60
days.
·
Unit
commanders/aviation
life
support personnel will ensure that
individual
emergency
type
parachutes, i.e., seat, back, chest, or
ejection seat type including drogue
chutes and harnesses when separate
from
the
parachute,
I.E.
chest
harnesses
and
ejection
seat
harnesses,
including
seat
belts,
when integrated into the harness
such
as
the
MK-J5D
parachute
system, will be inspected every 30
days by an individual qualified to
perform
30-day
parachute
inspections. These personnel will
have been trained in parachute
inspection methods by a qualified
parachute rigger. This training will
be documented in individual training
folders and designated as parachute
inspectors on unit orders by the
aviation unit commander.
·
Generic Description of Equipment
(1) Parachutes,
personnel,
emergency type: back, chest and
seat types.
(2) Parachutes,
personnel
and
drogue, ejection seat type.
(3) Harnesses, personnel parachute,
used with above parachutes.
b. Inspection Procedures. Inspection procedures
for personnel parachute assemblies and the MK-J5
ejection seat personnel parachute harness are explained
in the following paragraphs.
(1)
Personnel
parachute
assemblies.
Inspection procedures for emergency type personnel
parachute assemblies including back, seat, and chest
types are as follows:
(a) Remove DA Form 3912 from
assembly log record and survival manual pocket.
Check record for date of last pack. An emergency-
type personnel parachute which has exceeded 120
days (200 days for MK-J5 ejection seat parachute)
since the last pack will be considered unserviceable.
Process for repack according to step j. After
determining the last pack date, return the form to the
log record and survival manual pocket.
NOTE
An emergency type chest parachute
has two parachute log records. One
log
record
is
located
on
the
parachute pack, and the other is
found on the harness. Each of these
log records shall be maintained. On
an emergency type back parachute,
the log record may be located either
on the pack right wing flap or on the
pack bottom stiffener panel.
(b) Ensure that a copy of TM 10-
1670-1 is located in the log record and survival
manual pocket. On a chest parachute assembly, the
technical manual will be found in the pocket on the
parachute harness.
(c) Without
opening
the
pack,
visually check external condition of pack and harness
for defects or deterioration of webbing, canvas fabric,
or stitching, and broken or loose tacking.
(d) Check metal components for
cracks or rust. Check ripcord housing for dents or
breaks.
(e) Inspect the two canopy release
assemblies, if applicable, to ensure that each release
is assembled and locked properly.
(f) Inspect ripcord grip pocket to
ensure the ripcord grip is secure and the grip
protrudes enough to allow immediate accessibility.
Ensure that removal of ripcord is not obstructed by
misplaced stitching or tacking and that harness chest
strap on back parachute is not routed through ripcord
grip.
(g) Ensure that each pack opening
spring band is connected. Check the elasticity of each
band.
(h) Open ripcord protector flap and
inspect ripcord pins for proper seating in the pack
release cones. Ensure that pins are not bent or
corroded. On back of personnel parachute, each
ripcord pin shall extend 3/4 inch beyond pack release
cone (measuring from top of pin to eye of cone).
Change 1 11-27
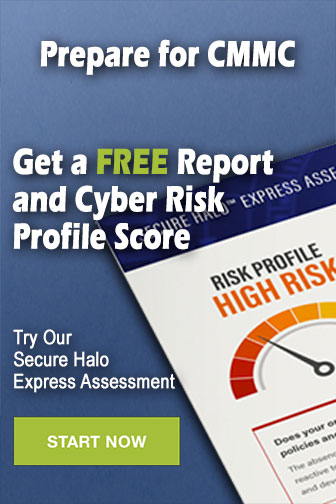