TM 1-1500-204-23-2
Table 4-29. Support Clamp Sizes (For use with MIL-H-38360 Hose of Teflon)
Hose Size
-3
-4
-5
-6
-8
-10
-12
-16
-20
Clamp Size
5
7
7
9
11
12
14
18
22
(MS21919)
(I)
Identification. Self-sealing aircraft hose or hose assemblies can be readily identified as to age and
manufacturer by code markings which are stencilled along the full length of the hose, at least 12 inches apart, placed
immediately adjacent to the color line (see figure 4-38). The cover of the hose will have a red stripe along its length
parallel to the longitudinal axis. The stripe maybe gum inlaid or gasoline and oil-resistant lacquer.
(2)
Inspection. Self-sealing hose and hose assemblies will be free from defects such as cracks, cuts,
breaks, blisters, looseness exposed braid, and restricted inside diameter. Surface irregularities such as mold marks,
laps, or air bubbles, as distinguished from cracks or cuts, shall not be cause for rejection.
(a)
Deterioration. Inspect hose as outlined n paragraph 4-5c (I)
(b)
Fittings. Inspect hose fittings as outlined paragraph 4-Se (2).
(3)
Design and construction. Hose shall be constructed of a seamless, smooth-bore, compounded inner
tube, a reinforcement, and an outer compounded cover. The hose shall be constructed as to permit ready assembly with
standard hose fitting connection ends, tubing ends, pipe threaded adapters, and hose clamps, conforming to AN 840,
MS28752, MS28753, MS28754, MS28755, MS28756, MS33660, MS33658, and MIL-C-6985, and Aeroquip kit part
number S-1051.
(4)
Hose assembly. Assemble hose as outlined in paragraph 4-5d.
(a)
Hose length. Determine correct hose length as outlined In paragraph 4-5d (4).
(b)
Assembly. Assemble hose and fittings, as outlined in paragraph 4-5h (5) and figure 4-43. (c)
Inspection. Inspect hose assembly Internally for cut or bulged inner tube (refer to table 4-30), obstructions, and
cleanliness. Inspect for proper gap between nut and nipple hex and socket
(5)
Identification tag. Hose assembly shall be identified as outlined In paragraph 4-5g.
(6)
Proof testing of hose assembly. All field-fabricated hose assemblies which have passed the visual
inspection shall be proof tested. Hose assemblies drawn from stock shall be inspected for defects such as mishandling
damage and proper banding, and proof tested if necessary. Proof testing procedures are:
(a)
Connect hose assembly to be tested to hydrostatic test unit, air supply, or nitrogen supply, as
appropriate, and apply correct pressure for hose assembly being tested. Proof pressure for MIL-H-706 I hose assembly
Is shown in table 4-3 1.
(b)
Observe hose assemblies proof tested with a liquid test medium for leakage from hose or around
fittings. Apply proof pressure for not less than 30 seconds and not more than 5 minutes.
NOTE
Tighten cap on hose assembly only after all trapped air has bled from the line.
(c)
Immerse hose assemblies proof tested with a gas test medium in water, and observe for leakage
from hose or around fittings. Apply proof pressure for not less than 30 seconds and not more than 5 minutes.
(d)
Reject hose assemblies showing evidence of leakage.
Change 1 4-73
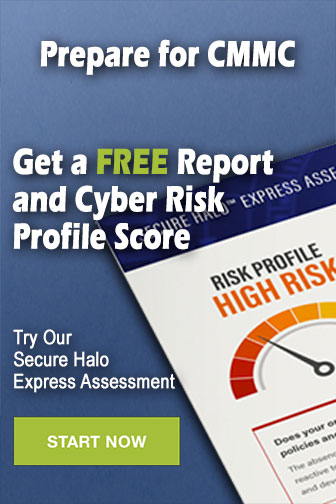