TM 1-1500-204-23-7
NOTE
Interference with navigation systems may occur if parts are not demagnetized after inspection.
a.
Reasons for Demagnetization. Aircraft ferromagnetic component parts require demagnetization principally to
prevent magnetic flux from affecting the instrumentation. This is the primary reason only and there are several
secondary reasons supporting demagnetization. These secondary reasons which follow are because the residual
magnetic field in a part:
May interfere with subsequent machining operations by causing chips to adhere to the surface of the part or the tip
of a tool which may become magnetized from contact with the magnetized part. Such chips can interfere with
smooth cutting by the tool, adversely affecting both finish and tool life.
May interfere with electric arc welding operations. Residual magnetic fields may deflect the arc away from the
point at which it should be applied.
May interfere with the functioning of the part itself, after it is placed into the service. Magnetized tools, such as
milling cutters, hobs etc., will hold chips and cause rough surfaces, and may even be broken by adherent chips at
the cutting edge.
May cause trouble on moving parts, especially those running in oil, by holding particles of metal or magnetic
testing particles-for instance, on balls or races of ball bearings, or on gear teeth.
May prevent proper cleaning of the part after inspection by holding particles magnetically to the surface of a part.
Demagnetization is likely to interfere with the magnetization of a part at a lower level of field intensity, not sufficient
to overcome the remnant field in the part.
May hold particles which interfere with later applied coating such as plating or paint.
b.
Conditions Not Requiring Demagnetization. Demagnetization is not required and is not usually carned out when:
Non-aircraft parts are of soft steel and have low retentivity. In this case, the residual field is low or disappears after
the magnetizing force is no longer acting. An example is low-carbon plate such as that used for low strength
weldments, tanks, etc
The metal in question consists of nonaircraft structural parts such as weldments, large castings, boilers, etc., where
the presence of a residual field would have no effect on other components or the proper service performance of
the part.
If the part is to be subsequently processed or heat-treated and in the process will become heated above the Curie
Point, or about 1418°(about 770°C). Above this temperature steels become nonmagnetic, and on cooling are
completely demagnetized when they pass through the reverse transformation.
The part will become magnetized anyway during a following process, as, for example, being held on magnetic
chuck.
A part is to be subsequently remagnetized in another direction to the same or higher level at which it was originally
magnetized as, for example, between the steps of circular and longitudinal magnetizing, for magnetic particle
testing purposes.
The magnetic field contained in a nonaircraft finished part is such that there are no external leakage fields
measurable by ordinary means; i.e., the testing by circular magnetization of welded and seamless pipe.
c.
Techniques for Demagnetization. Alternating and direct current are used in demagnetizing aircraft parts after
magnetic particle inspection. Although direct current can be used for demagnetization, alternating current
demagnetization has been found to be more convenient. Since alternating current does not penetrate very deeply below
the surface of magnetic metals, some parts may be difficult to demagnetize completely using alternating current. This is
particularly true with large heavy parts, and may also be the case
4-8
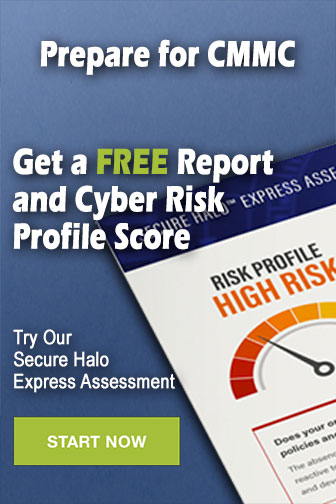