TM 1-1500-204-23-7
(1)
Selection of amperage. A number of factors must be considered when determining current amperage for
longitudinal magnetization of parts. Some of the more important factors are:
The coil diameter and the number of turns.
The length to diameter ratio of the part.
The size, shape, and composition of the part.
The orientation of position of the part within the coil.
The kind of discontinuities being sought and their ease of detection.
(2)
Coil shot amperage selection. Two rules of-thumb have been developed for use in determining coil
amperages to use for longitudinal magnetization. One is for a part centered in a coil and the other for when the part is
lying in the bottom of a coil. The rule-of-thumb formulas apply particularly to regular cylindrically shaped parts, the
diameters of which do not exceed about one tenth that of the coil (example: 1-1/4 inch diameter in a 12 inch coil) and the
part length to diameter ratio, (UD) does not exceed fifteen. Long parts having UD ratios greater than 15 must receive
more than one Inspection along their length since the most effective longitudinal field In a part only extends about nine
inches on each side of the coil. Amperages calculated using the rule-of-thumb formulas will produce in cylindrically
shaped steel parts a flux density of about 70,000 lines per square inch (10,850 gauss) which density is sufficient for
detection of most surface and near surface discontinuities. Refer to TM 55-1500-335-23 for other formulas.
(3)
Cable wrap coil. Cables used are commonly 2/0 or 4/0 AWG (American Wire Gauge), flexible stranded,
insulated copper cable. The number of turns used is kept low, from 3 to 5 turns, to minimize cable resistance in the case
of dc and coil impedance when ac is used.
c.
Applications. Longitudinal magnetization is used to inspect ferromagnetic components having material
permeabilities of about 500 or greater. This Includes most steel alloys. A simple test to determine whether or not a part
is magnetic is to place a permanent magnet against a part to be tested. If the pull or attraction of the magnet can be felt,
the part is sufficiently magnetic for magnetic particle inspection.
d.
Equipment A variety of equipment is available which can be used for either circular or longitudinal
magnetization. The equipment ranges in size from small general purpose portable units capable of being carried by
hand to large, custom-built stationary units with separate power supplies.
4-11. Magnetic Particle Indicators. Magnetic particle indication definitions and steps of Inspection are explained in the
following paragraphs.
a. Definitions. The operator who is to perform magnetic particle inspections should understand certain definitions
which are used in connection with this inspection method. These are defined in the following paragraphs.
(1)
Indication. In magnetic particle inspection, an indication is an accumulation of magnetic particles being
held by a magnetic leakage field to the surface of a part. The indication may be caused by a discontinuity (an actual void
or break in the metal) or It may be caused by some other condition that produces a leakage field.
(2)
Discontinuity. A discontinuity is an interruption in the normal physical structure or configuration of a part.
These discontinuities may be cracks, laps in the metal, folds, seams, inclusions, porosity, and similar conditions. A
discontinuity may be very fine or it may be quite large; it will generally be a definite separation or void in the metal.
(3)
Defect. A defect is a discontinuity which interferes with the usefulness of a part.
b.
Steps of Inspection. Magnetic particle inspection can be divided into producing an indication, interpreting the
indication, and evaluating the indication. Each is explained below in the following paragraphs.
(1)
Producing an indication. In order to produce a proper Indication on a part, it is necessary to have some
knowledge of the principles of magnetism, the materials used In inspection, and the technique employed.
(2)
Interpreting the indication. After the indication is created, it is necessary to interpret the indication.
Interpretation is deciding what caused that indication and what magnetic disturbance has attracted the particles in the
particular pattern found on the part. If the operator knows something about metal processing, it is possible to determine
from the appearance and location of an indication the cause of the indication.
4-6
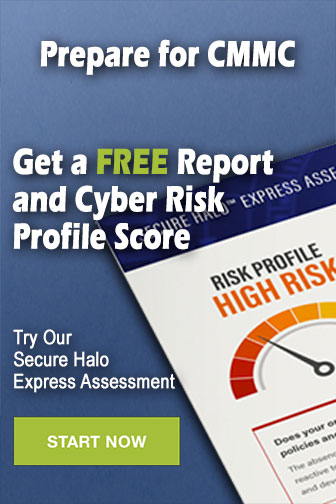