TM 1-1500-204-23-7
(b)
Compressed air gun application. Dry powder is also applied using hand held guns and compressed air.
One such device has the gun integral with the powder container and operates from an ordinary compressed air line.
Using the trigger, the operator controls the discharge of a powder cloud. Low velocity air removes excess powder to
better reveal indications. A more elaborate gun-type powder blower has a motor driven compressor integral with a
powder container and air-powder mixer. A multichannel rubber hose connects to the gun. A work light is contained in the
gun tip to illuminate the inspection area. A trigger on the gun controls the discharge of the powder-air mixture and blow-
off air. More elaborate production systems have been built using this same principle of operation. In these cases the
discharge nozzles are mechanically controlled as is the movement of parts through the machine. Spent powder is
automatically retrieved and reused.
(2)
Wet bath application. Many methods are used to apply wet bath magnetic particles. The methods range
from a simple hand pouring of a bath onto a part to large industrial systems in which the bath is applied automatically
either by dumping or spraying. The most common method for application is through the use of a hand-held nozzle and
recirculating pump on stationary units. Occasionally small, hand-held, lever operated sprayers are used. Aerosol-type
containers similar to those used to spray paint are also available.
WARNING
When using aerosol type spray containers, the area shall be well ventilated to prevent the build-
up of flammable vapors.
4-8. Current and Particle Application. Two methods of processing are used in magnetic particle inspection. The
method to use in a given case depends upon the magnetic retentivity of the part being inspected and the desired
sensitivity of the inspection to be made. Highly retentive parts may be inspected using what is called the residual
method. The continuous method must be used on parts having low retentivity. For a given magnetizing current or
applied magnetizing field, the continuous method offers the greatest sensitivity for revealing discontinuities a. Residual
Method. The residual method is a method of inspection in which magnetic particles are applied to parts after the parts
have been magnetized.
a.
Residual Method. The residual method is used only when parts are magnetized with dc. This method of
inspection is used only when parts have sufficient retentivity to form adequate magnetic particle indications at
discontinuities. This method is used with both longitudinal and circular magnetization techniques, either of which cause
the direct contact or central conductor method. Residual inspection requires the parts to be retentive enough to hold
magnetic particle Indications at discontinuities. Usually, the use of the residual method is limited to the search for
discontinuities which are open to the surface, such as cracks. Detection of subsurface discontinuities requires the
stronger leakage fields at discontinuities which exist while the part is being magnetized, as when the continuous method
is used. Residual inspection permits the magnetizing of parts at one time and the application of magnetic particle media
at some subsequent convenient time. When the central conductor method is used, inspection of holes or bores is
facilitated since Inspection takes place after removal of the central conductor.
b.
Continuous Method. This method implies that the magnetizing force is acting which the magnetic particles are
applied. When the current is on, maximum flux density will be created in the part for the magnetizing force being
employed. In some cases, usually when ac or half-wave dc is the magnetizing current being used, the current is actually
left on, sometimes for minutes at a time, while the magnetic particles are applied. This is more often needed in dry
method application than in wet. Leaving the current on for long durations of time is not practical in most instances nor is
it necessary. The heavy current required for proper magnetization can cause overheating of parts and contact burning or
damage to the equipment if allowed to flow for any appreciable length of time. In practice, the magnetizing current is
normally on for only a fraction of a second at a time. All that is required is that a sufficient number of magnetic particles
are in the zone and are free to move while the magnetizing current flows. The bath ingredients are so selected and
formulated that the particles can and do move through the film of liquid on the surface of the part and form strong,
readable indications. This is one reason why the viscosity of the bath and bath concentration are so important, since
anything that tends to reduce the number of available particles or to slow their movement tends to reduce the build-up of
indications.
c.
Field Direction. The proper orientation of the magnetic field in the part in relation to the direction of the defect is
a more important factor than the value or amount of the magnetizing current. For reliable inspection, the magnetic lines
of force should be at right angles to the defect to be detected. If the magnetic lines of force are parallel to the defect
there will be magnetic leakage at the defect and therefore, if any indication is formed it is likely to be extremely small.
4-3
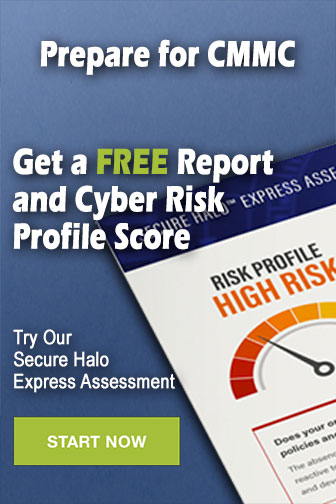