TM 1-1500-204-23-7
(1)
Selection of amperage. A number of factors must be considered when determining what current amperage
to use for circular magnetization. Some of the more important of these factors are:
The type of discontinuity being searched for and its expected ease or difficulty of being found.
The part size, shape and cross-sectional area through which the current will flow.
The amount of heating that can be tolerated in the part at the current contact areas.
(2)
Direct contact amperage selection. A rule of thumb suggesting 1,000 amperes per inch of part diameter is
useful when the part is reasonably uniform and cylindrical in shape. Except for some special alloys and cast irons, the
use of 1,000 amperes per inch of diameter will usually assure more than enough field strength to detect surface and near
surface discontinuities. In highly permeable material, lower amperage per inch of diameter will produce an adequate
field strength within the part.
(3)
Central conductor amperage selection. Amperage requirements using a central conductor will depend
upon the part size and the diameter of the opening through which the conductor is to be located. In the case of a
centrally located conductor, amperage requirements may range from 100 amperes per inch of hole diameter to as much
as 1000 amperes per inch depending upon part material and the nature of the suspected discontinuities. A reasonable
amperage figure to use is 500 amperes per inch of hole, bore or opening diameter. This should be sufficient for the
detection of surface type discontinuities on the inside of such openings. Keeping in mind that the magnetizing field
strength around a central conductor decreases with distance away from the conductor, higher amperages than these are
required to detect discontinuities which lie on the outside of a part. This limits the wall thickness that may be inspected
on the exterior to approximately 1/2 inch. Not only discontinuities which are parallel with the central conductor are
detectable using the central conductor method, but radial discontinuities at the ends of holes and openings can be
detected since some portion of the magnetic lines of force will Intercept these discontinuities.
4-10. Longitudinal Magnetization. Longitudinal magnetization is used for the detection of circumferential
discontinuities which lie in a direction transverse to, or at approximately right angles to a part axis. Circumferential
discontinuities around a cylinder for example, are detected by magnetizing the cylinder longitudinally in a direction
parallel with its axis. A portion of the longitudinal field will cross the discontinuities creating leakage fields which can
capture and hold magnetic particles to form indicators at the discontinuities
a.
Technique. Longitudinal magnetization is accomplished in a number of ways, magnetization in a coil being
the most widely used method. Parts can be magnetized longitudinally by placing them between the pole pieces of a pair
of electromagnets with the fields of the tow electromagnets being directed in the same direction through the part. Still
another method is the magnetizing of parts between the feet of yoke or prove using either the electromagnetic or
permanent magnet type.
(1)
Coil shot. The usual way to longitudinally magnetize a part is to place the part in a rigid coil in a stationary
magnetic particle inspection unit. The part may be laid on the bottom inside of the coil where the field is strongest or the
part may be supported in the coil by the contact heads of the units for long heavy parts permitting rotation of parts for
inspection Coils are usually mounted on rails permitting movement along a long part for multiple inspections (multiple
coil shots). Because the effective field extends only six to nine inches on either side of a coil, multiple inspections are
needed on long parts.
(2)
Cable wrap. Cable wrapping a coil around large or heavy parts is a common practice. Flexible, insulated
copper cable Is used. A cable-wrapped coil is connected to a magnetic particle mobile or portable power pack or it can
be connected to the contact heads of a stationary Inspection unit. The type of power source to be used will depend upon
the kind of current and amperages needed to magnetize the part for the particular desired inspection, and then
demagnetize it.
b.
Amperage. The magnetizing field strength in the center of the magnetizing coil, increases or decreases with
either the coil current or its number of turns. It can also be seen that the field strength will decrease if the coil radius Is
made larger or will increase if the radius is made smaller. The field is theoretically zero in the coil center and increases
to a maximum at the inside edge of the conductor. Thus a part placed against the inside of a coil, for example lying in
the bottom of the coil, will experience a greater magnetizing field strength than when it is centered in the coil.
4-5
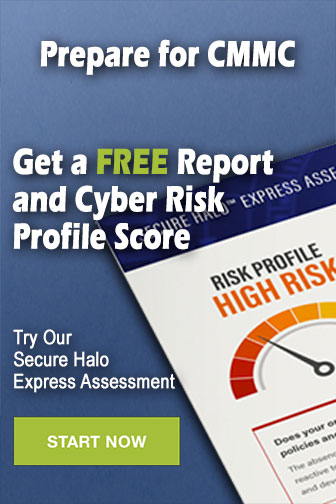