TM 55-4920-328-13
a.
Check
the
operation
of
the
suspect
transmitter (11MT1 or 11MT2) as outlined in paragraph
58. Alternately, an operational check may be performed
on the system level by substitution of the suspect
transmitter with another transmitter of like part number.
b.
Energize the METS electrical systems as
outlined in chapter 2, Preliminary Checkout Prior to Test
paragraph. Allow the specified 30-minute warm-up and
stabilization period.
c.
Check the output of power supply 4A12PS5,
which must be 28+lv dc. If there is no dc output at this
component, check for the presence of 117v ac, 60 Hz at
4A12PS5-1 and -2.
d.
With 28v dc excitation power available at
11P1-A and -D and at 11P2-A and -D, interchange
transmitters 11MT1 and 11MT2 to determine if the fault
still exists in the suspect circuit.
5-30. Oil Pressure System.
Troubleshoot the oil pressure system using the
circuit information shown in figure FO-13 and as follows:
NOTE
It is assumed that continuity and power
voltage levels have been checked prior to
accomplishment of the following.
a.
Check the suspect pressure transmitter as
outlined in paragraph 5-10.
b.
Check the switching circuits depicted in figure
FO-27.
c.
Follow the general procedural steps specified
in paragraph 5-27.
5-31. Engine Low Oil Pressure System.
Troubleshoot the engine low oil pressure system
using the circuit information shown in figure FO-20,
figure 5-35 and check the suspect pressure switch as
outlined in paragraph 5-15.
NOTE
It is assumed that continuity and power
voltage levels have been checked prior to
accomplishment of the following.
5-32. NI and NII Speed System.
Since the speed system operates on a signal input
from a tachometer generator (the engine output shaft
speed
signal
is
proportional
to
frequency),
no
measurable voltage level is available for fault isolation
in the signal circuits to meters M2 and M3 on operator's
panel assembly. The vertical tape indicator input signal
Is in the form of a 0 to 5v dc analog which is
measurable with a dc voltmeter. Therefore, if an analog
above 0v dc is available at 1A3-1W12P1-V and -U, and
at 1W12P1-X and -W, it must be assumed that the
applicable circuits through engine safety unit 3A4 are
intact. The signal input to speed monitor chassis
assembly 2A1 is in the form of a + pulsed signal
proportional to 6 times the tach frequency. The speed
monitor chassis assembly may be isolated from the
system and tested by the self-test function of the unit.
(Refer to chapter 2.) It is recommended that the speed
system calibration procedures be simplified as an aid in
troubleshooting. Check for approximately 2.5v dc af
4J1-M and -D, (services sub-module) observing polarity,
to isolate a faulty monitor alarm assembly. If erratic
signals are observed on the speed monitor chassis
assembly, clean the circuit board connector contacts as
outlined in chapter 6. If this action does not clear the
trouble, check the installation of each tachometer
generator as outlined in chapter 2. Check each
tachometer generator by the substitution method if the
trouble persists, then replace the faulty component.
Two six times (6X) multipliers are located in engine
safety unit 3A4. One each is used in each of the speed
channels to provide six pulses out for each pulse in.
The three phase input from the tachometer is multiplied
by six and used as the input to the digital speed
indicator.
Better
resolution
for
conversion
to
engineering units is obtained due to the multiplication.
The tach-generator output at 100% is 70 Hz.
Using the input to the six times multiplier, the output to
the digital indicator would be 420 Hz. Utilizing the "K"
factor pre-set of 2,381 as the multiplier, the output
Indicated on the digital indicator would be 100.0. The
decimal point on the digital indicator is fixed.
5-33. T55-L-7/11/712 Electrical Torque System
(Using Avco Inverter P/N 211900).
Proceed as follows:
a.
With all systems connected and energized
and the specified warm-up accomplished, check the
current and frequency output of the inverter. The
current must be 557 + 2 ma at 2K Hz, checked as
follows:
(1)
Remove connector PB from the mating
connector on the inverter.
Change 4
5-31
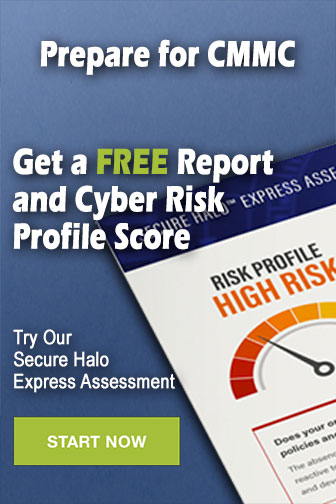