TM 55-4920-328-13
(2)
Connect a jumper between corresponding
pins A, B, and C in P8 and the inverter.
(3)
Connect a jumper to pin D in the inverter and
to a 1-ohm precision resistor. Connect the precision
resistor to P8-D using another jumper.
(4)
Connect an rms voltmeter across the 1-ohm
resistor to observe the voltage drop.
(5)
With the engine torque transmitter electrically
connected into the circuits to the T55-L-11/712 indicator
and to the inverter, the voltage drop across the resistor
must be 557 + 2 mv ac rms.
(6)
Remove the resistor and jumpers, then
restore the circuitry as shown in figure FO-16.
b.
For T55-L-7 model engines, adjust the
indicator to display electrical zero (connected with no
input) by use of the zero adjustment potentiometer on
the rear of the indicator housing.
c.
Deenergize all system power.
d.
Replace defective components using good
shop practice. Recheck as required.
5-34. Torque Element System.
Troubleshooting of the torque element system
(figure FO-17 and 5-18) is conducted as follows:
a.
Accomplish a self-test of temperature and
torque/pressure indicator 1Al as outlined in chapter 2.
Preliminary Checkout Prior to Test paragraph.
NOTE
The
applicable
torque
system
must
be
installed and operating to accomplish the
following.
b.
At approximately 10v dc excitation power
applied to 11J12-B and -C, the signal output of 11J12-
A(+) and -D(-) must be 1.5 millivolts per volt of
excitation at 100% torque for T53 and T55 torque
elements. The signal output at these points must be 0.5
millivolt per volt of excitation at 100% torque when the
T63 torque system is installed.
c.
The output of vertical tape indicator assembly
1A3 at J2-y(+) and -x(-) must be 0 to 0.5v dc (5k
element), 0 to 3v dc (30k element), or 0 to 6v dc (60k
element) at 100% torque.
5-35. Fuel System.
Troubleshoot the fuel system (figure FO-19) as
follows. After continuity, power voltage levels, and test
points have been checked, no other component checks
may be conducted. The fuel flowmeter provides a
signal to fuel flow signal conditioner 2A9A1 in the form
of a sine wave signal. The signal conditioner output is
in the form of a usable frequency proportionate to flow.
The output of the signal generation and conditioning
units cannot be measured with common test equipment.
Therefore, these units may be checked by the
substitution method to isolate the faulty unit. The fuel
flow/consumption monitor chassis assembly 2A2 is
provided with a self-test capability, which will indicate
the pre-set "k" factor when placed in the TEST position.
The modulated carrier type of turbine flowmeter should
not be confused with the Magnetic type, which has the
same physical appearance. The system may be
functionally checked by the substitution of another
flowmeter unit. The direction of flow must be observed
when installing a new unit.
Calibration of the Modulated Carrier flowmeter
cannot be accomplished on-site, and must be removed
and forwarded to a Depot with carrier type calibration
capability, as required in the Calibration TB.
5-36. Services Oil Flow System.
Accomplish the general procedures outlined in
paragraph 5-35 to troubleshoot the services oil flow
system (figure FO-20).
5-37. Vibration System.
Troubleshoot the vibration system (figure FO-21
and 5-24) as follows:
a.
After power input and continuity checks have
been accomplished, check the vibration pickup as
outlined in paragraph 5-14. Interchange the units to
isolate a defective pickup.
b.
Accomplish the daily calibration of vibration
meter 2A3 as specified in chapter 2, Multi-Channel
Vibration Meter paragraph.
5-38. Throttle Position and IGV Indicating System.
Troubleshoot the TP1 and IGV system (figure FO-
22 and 5-27) by the substitution method. Proceed as
follows:
a.
With the electrical systems energized, install
and electrically switch the position transmitters from the
normal installation.
PIN: 038052-004
U.S. GOVERNMENT PRINTING OFFICE: 1989 654-030/00035
Change 4
5-32
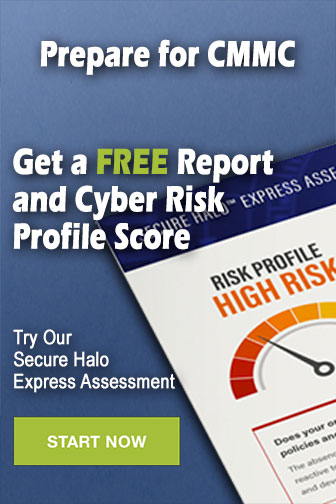