TM 1-1500-204-23-1
CHAPTER 9
GENERAL AIRFRAME MAINTENANCE
9-1. General. The maintenance instructions and
procedures contained in this chapter are general and
applicable to airframe maintenance of Army aircraft.
Maintenance instructions that are specific and peculiar
to particular airframes are contained in the applicable
maintenance manuals and will be used in conjunction
with general information contained in this chapter.
9-2. Landing Gear Systems. The landing gear of an
aircraft consists of main and auxiliary units, either of
which may or may not be retractable. The main landing
gear forms the principle support of the aircraft on land or
water and may include any combination of wheels,
floats,
skis,
shock-absorbing
equipment,
brakes,
retracting
mechanism
with
controls
and
warning
devices, cowling, fairing, and structural members
necessary to attach any of the foregoing to the primary
structure. The auxiliary landing gear consists of tall or
nose wheel Installations, outboard pontoons, skids, etc,
with necessary cowling and reinforcement
9-3. Retractable Landing Gear Systems. Retractable
landing gear systems are explained in the following
paragraphs.
a.
Types. The electric and hydraulic landing gear
retraction systems are explained in the following
paragraphs.
(1) Electric landing gear retraction system. The
electric landing gear retraction system is an electrically
driven jack for raising or lowering the gear, as shown in
figure 9-1. When a switch in the cockpit is moved to the
UP position, the electric motor operates. Through a
system of shafts, gears, adapters, an actuator screw,
and a torque tube, a force is transmitted to the drag strut
linkages. Thus, the gear retracts and locks If the switch
is moved to the DOWN position, the motor reverses and
the gear moves down and locks.
(2) Hydraulic landing gear retraction system.
Devices used In a typical hydraulically operated landing
gear retraction system include actuating cylinders,
selector valves, uplocks, downlocks, sequence valves,
turbine, and other conventional hydraulic components.
These units are interconnected so that they permit
properly sequenced retraction and extension of the
landing gear and the landing gear doors. Figure 9-2
shows a typical hydraulic landing gear retraction system.
b.
Emergency Extension Systems. The emergency
extension system lowers the landing gear if the main
power system fails. Some aircraft have an emergency
release handle in the cockpit, which is connected
through a mechanical linkage to the gear uplocks.
When the handle is operated, it releases the uplocks
and allows the gear to free-fall, or extend, under their
own weight. On other aircraft, release of the uplock is
accomplished using compressed air which IS directed to
uplock release cylinders. Some installations are
designed so that either hydraulic fluid or compressed air
provides the necessary pressure, while others use a
manual system for extending the landing gears under
emergency conditions. Hydraulic pressure for
emergency operation of the landing gear may be
provided by an auxiliary hand pump, an accumulator, or
an electrically powered hydraulic pump, depending upon
the design of the aircraft.
c.
Safety Devices. Accidental retraction of a
landing gear may be prevented by such safety devices
as mechanical downlocks, safety switches, and ground
locks. Mechanical downlocks are built-in parts of a
gear-retraction system and are operated automatically
by the gear-retraction system. To prevent accidental
operation of the downlocks, electrically operated safety
switches are Installed.
(1) Safety switch. A landing gear safety switch,
as shown In figure 9-3, in the landing gear safety circuit
is usually mounted in a bracket on one of the main gear
shock struts. This switch is actuated by a linkage
through the landing gear torque links. The torque links
spread apart or move together as the shock strut piston
extends or retracts in its cylinder. When the strut is
compressed (aircraft on the ground), the torque links are
close together, causing the adjusting links to open the
safety switch. During takeoff, as the weight of the
aircraft leaves the struts, the struts and torque links
extend, causing the adjusting links to close the safety
switch. As shown in figure 9-3, a ground is completed
when the safety switch closes. The solenoid then
energizes and
9-1
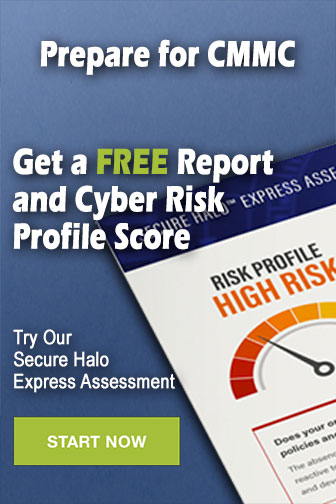