TM 1-1500-204-23-2
m.
Instructions for Field Assembly of Lightweight Rubber Hose Assembly MIL-H-83796/1 thru MIL-H-83796/9.
Lightweight hose assemblies are fabricated from bulk hose conforming to MIL-F-83978, and are used for fuel and oil
systems. The lightweight hose assemblies are not recommended for vacuum or hydraulic Impulse application.
(1)
Inspect hose as outlined In paragraph 4-5e (1).
(2)
Inspect fittings as outlined In paragraph 4-5e (2)
NOTE
Because of contamination by foreign matter or unseen damage and wear, and because parts of fittings from
different manufacturers are not interchangeable, do not salvage or reuse fittings.
(3)
The listed equipment and material are required for field assembly.
·
Shop vise
·
Fine tooth hacsaw
·
Masking tape
·
10,000 psi hydrastatic test machine.
·
Standard wrenches
·
Feeler gage
·
Measuring tape
(4)
Determine length of hose required to make assembly length "L" by use of cut-off notices on the socket
Refer to step 1, figure 4-50A.
(a)
When required to fabricate a new hose assembly without any sample, drawing, or other data to
determine length requirements, check the aircraft parts manual for a Military Specification (MS) identification number.
An MS number contains a code which depicts the size of tube, length of assembly, and types of fittings. In absence of
any of the foregoing, proceed as follows:
1
From the aircraft parts manual, find the figure which shows location and general position of
hose.
2
With the fittings loosely assembled in their proper position on the aircraft, cut a piece of
hose approximately three inches longer than will be required.
3
Hold or tape one end of hose even with groove of one nut, and maneuver the remainder of
hose into a final position over other nut. Mark required length as determined by groove of second fitting and cut to size.
CAUTION
A hose too short will put too much tension on assembly, or a hose too loose will flap and possibly become
chafed.
4
Fabricate hose assembly per instructions.
(5)
Cut Hose Equally to Length. Use hose cut-off machine or fine-tooth hacksaw. To minimize wire braid
flare-out, wrap hose with masking tape and saw through tape. Refer to step 2, figure 4-50A. Remove tape before doing
step 3 Check to see that no wire of outside braid has become bent over end of hose.
(6)
With socket in a vise as shown step 3, figure 4-50A, insert hose into socket.
NOTE
Use a twisting, pushing motion to push hose into socket to a depth equal to cut-off notch A dimensional check
must be made to insure that hose is inserted to a proper depth.
4-74.2 Change 2
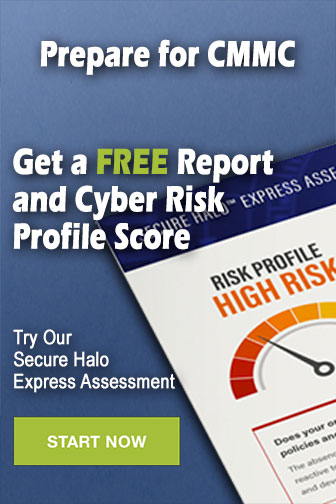