TM 1-1500-204-23-2
4-11. Hydraulic Reservoirs. The system reservoir hold enough fluid for use in operation of the system and to replace
fluid lost through minor leakage or evaporation. Reservoirs may also be Installed to provide a space for increase in fluid
volume over the original amount, such as that which might occur through thermal expansion or foaming They also
provide a place of escape for air trapped in the system.
a.
Types of Reservoirs Used in Hydraulic Systems. Two types of reservoirs are used in aircraft hydraulic systems
the in-line and the integral type.
(1) In-line. The in-line reservoir, seen in figure 4-91, has its own housing, is complete within itself, and is
connected with other components in the system by tubing or hose. The in-line type is most common in Army aircraft, and
is covered in this manual.
(2) Integral. The integral reservoir consists merely of a space set aside within a major component for the
purpose of holding a supply of operational fluid. An example of this kind of reservoir is an automotive brake master
cylinder.
Figure 4-91. Reservoir with Baffles, Fins and Finger Strainer
b.
Theory of Operation. A space is provided in the reservoir above the normal level of the fluid for fluid expansion
and for escape of trapped air. Most reservoirs are designed so they cannot be serviced completely to the top. This Is
done by locating the filler neck somewhat below the top of the reservoir. On most reservoirs, a dipstick or glass sight
gauge is provided so that fluid level can be easily and accurately checked. All reservoirs are either vented or closed to
the atmosphere and pressurized.
(1) Vented reservoirs. In vented reservoirs, atmospheric pressure and gravity are the forces which cause fluid to
flow out of the reservoir and into the pump. In order to supply a pump with fluid, a vented reservoir must be positioned at
a higher location than the pump. If the reservoir and the pump were at the same level, gravity would have no effect on
fluid flow. If the reservoir was at a level below the pump, fluid would tend to run out of the pump and into the reservoir
Most hydraulic system reservoirs of current Army aircraft are vented.
(2) Pressurized reservoirs. In the hydraulic systems of some aircraft, it is necessary to mount the reservoir at a
level below the pump In this case, the weight of the fluid obviously deters, rather than aids, the flow of fluid into the
pump. A reservoir so located has to have the fluid it contains under greater than atmospheric pressure to force the fluid
upward into the pump. Another reason for pressurizing reservoirs is to enable aircraft to fly at very high altitudes Since
atmospheric pressure decreases as altitude increases and at very high altitudes become too low to force enough fluid
into a pump, the reservoir has to be pressurized Two general methods of pressurizing reservoirs are employed One
method employs fluid, the other air.
(a) Fluid-pressurized reservoir. This method makes use of fluid pressure bled from the pressure lines of the
system In which the reservoir is Incorporated The reservoir is designed In such a way as to develop a relatively low
pressure on the supply fluid contained in the reservoir by use of a stream of fluid fed Into the reservoir at a much higher
pressure Such a reservoir is commonly called an airless reservoir.
1
Construction Figure 4-92 shows the construction and operation of a typical reservoir
pressurized In this manner. The major parts of the assembly are a cylindrical housing that has three fluid ports and a
polished bore, a housing tube which terminates in a head, and a piston and piston tube assembly The piston and piston
tube assembly are free to slide back and forth
4-102
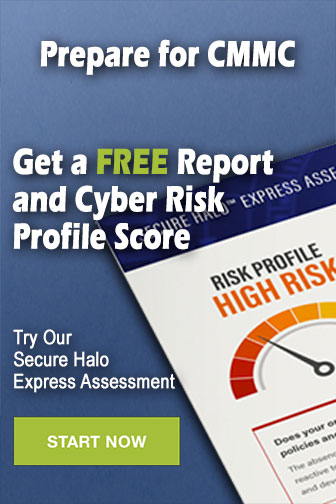