TM 1-1500-204-23-2
2
Activation of flyweight governor. Movement of the wobbler plate also
momentarily activates the preact piston (2) of the flyweight governor This prevents over-travel of the governor control
valve and hastens the motor's response to changes in load. The preact piston acts when the wobbler plate moves to the
right and the control piston moves to the left. This action forces fluid in the feedback line (10) into the chamber on the
left side of the preact piston When fluid moves into this chamber, the preact piston moves to the right, increasing tension
on the governor spring (1) and opposing movement on the governor control valve to the left. Motor speed decreases and
the fluid in the preact piston chamber bleeds off through the restrictor bleed. The governor control valve moves back to
the right, blocking the control piston passage and holding the wobbler plate in its new position. These events occur
almost instantly to match torque requirement with the load.
3
Back pressure valve. A back pressure valve (5) is installed in the discharge line
of the lower piston to prevent the piston from floating and chattering. If this valve were not In the return line, return
pressure would exist on both sides of the lower pistons. Under this condition, the pistons would tend to float. The back
pressure valve puts 100 psi over return pressure load on the back side of the lower pistons. This load holds them against
the wobbler plate and prevents chattering.
(3)
Maintenance. Repair and overhaul of hydraulic motors are done at depots. This work requires
special tools and equipment.
4-14.
Devices for Regulating Pressure. Devices for regulating pressure in aircraft hydraulic systems include
pressure gauges, pressure switches, relief valves, and pressure reducing valves.
a.
Pressure Gauges. Hydraulic pressure gauges indicate the amount of pressure in a hydraulic system.
Gauge dials are calibrated to display this pressure in pounds-per square inch (psi). Direct-reading and remote-indicating
gauges are the types used.
(1)
Direct-reading gauges. The direct-reading gauge shown in figure 4-114 consists essentially of a
Bourdon tube, a pointer, a dial, and a raintight case. The Bourdon tube and the pointer are interconnected by gearing to
cause them to move together. Pressure within the hydraulic system is admitted into the Bourdon tube through a
connecting line. As hydraulic system pressure increases, it causes the Bourdon tube to straighten to a corresponding
degree. The change in curvature of the tube reacts on the gearing, causing the pointer to move to a correspondingly
higher reading on the dial. As hydraulic system pressure decreases, the Bourdon tube curls back toward its original
shape by a corresponding amount. This causes the pointer to fall back to a correspondingly lower dial reading. Pressure
gauge snubbers are usually used with hydraulic pressure gauges to dampen oscillations of the pointer.
(2)
Remote-indicating gauges. In the remote-indicating gauge, the gauge transmitter contains a
Bourdon tube diaphragm, or bellows, to which hydraulic system pressure is admitted through a connecting line. The
Bourdon tube diaphragm reacts to pressure changes in a manner similar to that of the direct-reading type gauge.
Movements of the diaphragm produce electrical signals that are transmitted through connecting wiring to the indicator
unit, where they cause the indicator pointer to move. Some aircraft systems have a direct-reading gauge in a location in
the system in addition to a remote-indicating gauge In the event a remote-indicating gauge indicates a possible problem,
always check the direct-reading gauge to confirm whether the gauge or the system is at fault.
b
Pressure Switches. A pressure switch is designed to open or close an electrical circuit in response to a
predetermined hydraulic pressure entering the switch from a connected source Piston-type and diaphragm-type pressure
switches are the types commonly used in Army aircraft.
(1)
Piston-type. The piston-type pressure switch shown in figure 4-115 consists of a rectangular
shaped housing, a cylinder bore and piston, an adjustable spring for loading the piston, a microswitch and a linkage for
transmitting movement of the piston to the microswitch. The housing has a port for connecting the switch to a system
pressure line and an electrical receptacle for connecting the switch with an electrical circuit.
(2)
Diaphragm-type. The diaphragm -type pressure switch consists of a cylindrical-shaped housing
a diaphragm, an adjustable spring to load the diaphragm, a microswitch, and linkage for transmitting movements of the
diaphragm to the microswitch. The housing has a port at one end for connecting the switch to a system pressure line and
an electrical receptacle for connecting the switch with an electrical circuit at the other end.
(3)
Operation. The operation described here covers the piston-type pressure switch. However, the
diaphragm switch operates on essentially the same
4-121
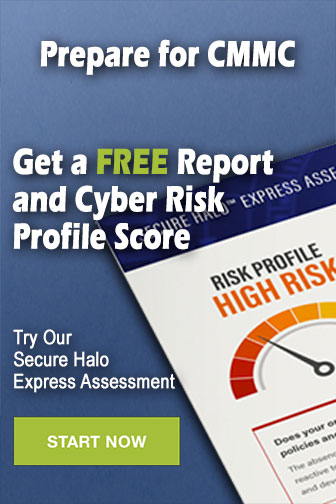