TM 1-1500-204-23-2
air pressure has been exhausted through the valve core or the valve core has been removed from the air valve
assembly. The hydraulic system pressure gauge will indicate the approximate accumulator air pressure when the
hydraulic hand pump has been operated for a period of time starting with zero pressure on the hydraulic system.
b.
Accumulator Operation. Spherical and cylindrical accumulators operate in essentially the same manner.
In operation, the compressed-air chamber is charged to a pressure somewhat lower than the system operating pressure.
This initial charge is referred to as the accumulator preload. When a preload is Introduced in an accumulator, the
hydraulic system pressure will be zero. As the system is subsequently pressurized and overcomes the preload pressure,
the air will be compressed in the accumulator. When use of hydraulic units lowers system pressure, the compressed air
will then force fluid from the accumulator into the system to satisfy system demands. Many aircraft have several
accumulators in the hydraulic system. There may be an accumulator for the main and emergency systems, and there
may be auxiliary accumulators located in venous unit systems.
c.
Maintenance.. Maintenance of accumulators at the organizational and Intermediate maintenance levels
primarily consists of inspection and servicing. Some intermediate maintenance activities may have the responsibility for
overhaul or repair, but this primarily rests with the depot maintenance units Inspection and servicing procedures are as
follows.
(1)
Visually inspect accumulators for indications of external hydraulic leaks.
NOTE
Use only dry air or nitrogen when pressurizing accumulator.
(2)
Test for internal leaks by momentarily depressing the valve core.
NOTE
On cylindrical type accumulators, a slight amount of atomized hydraulic fluid is permissible. When
liquid fluid escapes from the air valve, excessively worn seals or a scored piston are indicated and
replacement of the accumulators necessary.
On spherical type accumulators any indication of fluid at the air valve shall be cause for replacement
of the accumulator, as this is an indication of deterioration or rupture of the diaphragm.
(3)
Check the preload pressure on the accumulator by depleting the fluid pressure. This may be
done by operating the controls of a system of which the accumulator is a part until all reserve pressure has been used.
(4)
Ensure that the air preload is completely exhausted before disassembling the accumulator.
4-16.
Flow Control Units . Numerous valving devices are used in aircraft hydraulic systems to control the flow of fluid
within the system. These devices perform such functions as controlling direction, sequence, and priority of flow;
transforming fluid pressure into mechanical energy; holding loads in position against feedback-induced forces; and
preventing leaks. The devices that perform these functions are selector valves, control valves, check valves, sequence
valves, priority valves, shuttle valves, actuating cylinders, ratchet valves, servos, irreversible valves, and fuses.
a.
Selector Valves. The purpose of a selector valve is to control the direction of movement of an actuating
unit. It does this by providing pathways for pressure and return fluid into and out of an actuating unit, and by providing
the means for immediately and conveniently switching the directions of the pressure and return fluid (necessary for
reversing the direction of movement of the actuating unit). Selector valves are classified as closed-center and open-
center types. These classifications are based on what happens to the flow of fluid when the selector valve is placed in
the off position. When a closed-center selector valve is placed in the off position, its pressure passage is blocked to the
flow of fluid and no fluid can pass through its pressure port. When an open-center selector valve is placed in
4-124
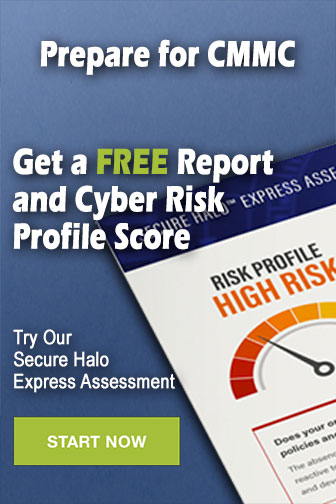