TM 1-1500 204-23-2
principles. Fluid pressure entering the port of the pressure switch acts on the face of the piston to move it against the
resistance of the piston return spring. When the fluid pressure acting on the piston becomes great enough to overcome
the force of the piston return spring, movement of the piston causes the pivoted lever of the connecting linkage between
the piston and the micro-switch to rotate. The movement of the pivoted lever is transmitted through the Idler spring to
the actuating button of the microswitch. When the microswitch actuating button has moved a sufficient amount, the
micro-switch contacts move into the pressure-induced position. Some pressure switches are designed so that their
contacts remain open until closed by the action of fluid pressure against the switch position. Such switches are specified
as NORMALLY OPEN (NO). Other switches are designed for their contacts to remain closed until opened by the
reaction of fluid pressure against the switch piston. These are specified as NORMALLY CLOSED (NC).
(4)
Uses. Pressure switches on Army aircraft serve two purposes. One is to close the circuit of a
warning fight that shows low pressure in a system. The other is to affect the circuits of solenoid valves in aircraft having
dual hydraulic boost control systems in such a manner that operating pressure to one boost system cannot be shut off
unless the other boost system is provided with enough operating pressure to fly the aircraft. Some pressure switches are
designed with two sets of contacts so as to provide control for both the warning light and the solenoid valve.
(5)
Maintenance. Maintenance of hydraulic pressure switches is limited to testing, removal, and
replacement.
c.
Pressure Relief Valves. Relief valves are safety devices used to prevent pressure from building up to a
point where it might blow seals and thus burst or otherwise damage the container in which it is installed. Relief valves
are installed in aircraft hydraulic systems to relieve excessive fluid pressure caused by thermal expansion, pressure
surges, and the failure of a hydraulic pump compensator or other regulating devices.
(1)
System relief valves. Main system relief valves are set to open and close at pressure
determined by the system in which they are installed. In systems made to operate at 3,000-psi normal pressure, the
relief valve might be set to be completely open at 3,650 psi and to reseat at 3,190 psi. These pressure ranges may be
different from one aircraft to another. When the relief valve is in the open position, it sends excess pressurized fluid to
the reservoir return line.
(a)
Description. A typical main system relief valve and a breakdown of its component parts
is shown in figure 4-116. The relief valve consists of a cylindrical housing containing a poppet valve and a piston
assembly Each end of the housing is made to include a wrench-holding surface and a threaded port for installation of a
hydraulic fitting. The housing is stamped to Denny the ports as PRESS (pressure) and RET (return). The poppet valve
(1), which is located just inside the pressure port, is seated over a passage through the valve.
(b)
Operation. When fluid pressure at the pressure port reaches 3,650 psi, the pressure
forces the piston (2) to depress the load spring (3) and to move clear of the poppet valve. Thus, the passage through the
piston is opened, and fluid flows through the valve into the return line. When pressure at the pressure port is reduced to
3,190 psi the coil spring reseats the piston against the poppet valve and fluid flow through the relief valve ceases.
Should the pressure at the outlet port exceed the pressure at the inlet port, the poppet valve will unseat and fluid from the
return line will flow through the valve into the pressure line.
(2)
Thermal relief valves. Thermal relief valves are usually smaller than system relief valves. They
are used in systems where a check valve or a selector valve prevents pressure from being relieved through the main
system relief valve. As pressurized fluid in the line in which it is installed builds up to an excessive amount, the valve
poppet is forced off its seat and the excess pressurized fluid flows through the relief valve to the reservoir. When system
pressure decreases to a preset pressure, spring tension overcomes system pressure and forces the valve poppet to the
closed position.
(3)
Maintenance. Relief valve maintenance is limited to adjusting the valve for proper relief
pressure and checking the valve for leakage. If it is thought that a relief valve is leaking internally a flexible hose may be
connected to the return port of the valve and the drippings, if any, caught in a container. The opening and closing
pressure of the valve may also be checked in this manner provided an external source of power is used.
d.
Pressure Reducing Valves. Pressure reducing valves are used in hydraulic systems where it is
necessary to lower the normal system operating pressure to a specified amount.
4-122
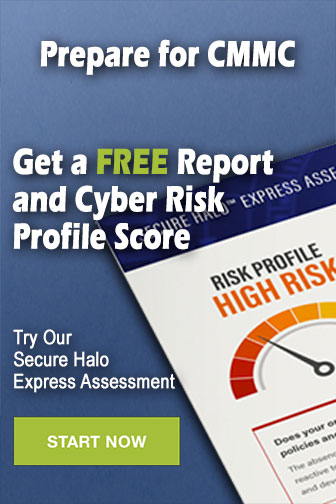