TM 1-1500-204-23-2
(d)
Testing. After the pump has been reassembled, test it for proof pressure and leakage.
Figure 4-112 illustrates a simplified setup for testing the hand pump.
1
Proof pressure. To test for proof pressure, pump fluid through the circuit with
the pump connected and the shutoff valve open. This bleeds all air from the system. Next, close the shutoff valve and
operate the pump to obtain the required proof pressure. Proof pressure is approximately 1-1/2 times normal operating
pressure. Control the strokes so that the final stroke will leave the piston in the retracted position, after which pressure
should be maintained for a specified time (usually 2 to 5 minutes). Repeat the preceding step, this time controlling the
strokes so that the final stroke will leave the piston in the extended position.
2
Leakage test. For the leakage test, use the pump to pressurize the circuit to the
normal operating pressure (the shutoff valve is closed during this check). The pressure must hold for a specified period
of time (approximately 2 minutes). There should be no piston creep, and the pressure drop should not exceed the
specified amount (usually 50 to 100 psi).
3
Completion of testing. After completion of testing, relieve the pressure and
remove the pump from the test circuit. Drain the pump to the drop point. Then refill it with the specified preservative
fluid to about 90 percent of its capacity. Plug all ports and closures and mark the rubber parts cure date of the pump
d.
Hydraulic Motors. Motors operate on the same principle as power pumps, but in reverse.
(1)
Applications. Figure 4-113 shows a variable-displacement, axial-piston, rotating-cylinder-block
unit. It delivers a minimum of 16.6 horsepower at 8,000 rpm. This particular motor is used to drive an ac-dc generator at
a constant rpm. Since an ac generator or alternator must put out the same number of cycles per second under all load
conditions, a very sensitive flyweight governor is required on the motor. For components where the rpm is not critical, a
constant-displacement-type hydraulic motor would probably be used.
(2)
Operation. When the hydraulic system is pressurized, fluid pressure is put on the pistons of the
cylinder block. Pressure must also go to the closed starting valve of the motor. Normal system pressure will sustain
cylinder and generator rotation, but higher pressure is needed to start the rotation.
(a)
Starting. Starting is accomplished by the starting valve (6). When system pressure
builds up to 1,800-2,200 psi, the starting valve is moved to the right as shown. This action permits fluid under pressure
to move the control piston (9). The control piston moves the bottom of the wobbler plate (8) to the right with sudden
force. Movement of the wobbler kicks the upper and lower pistons (7) to give the cyliner block an initial spin. Thereafter,
system pressure maintains rotation of the cylinder block. As hydraulic pressure continues to Increase, motor speed
increases. As the rotational speed increases, the governor flyweights (3) begin to pivot outward, moving the governor
control valve (4) proportionately to the left. This movement gradually block the pressure to the control piston. When the
passage is completely blocked, pressure is no longer put on the control piston and motor speed ceases to increase. This
is referred to as an on-speed condition.
(b)
Load control. The load imposed on the motor varies with the electrical load on the
generator. To meet the changing demands, the motor must vary its torque to maintain its normal operating speed. Let
us assume that the motor tends to overspeed.
1
Overspeed. The overspending causes the governor flyweights (3) to move
outward, pulling the governor control valve (4) a little bit to the left. Movement to the left from the blocked position vents
the control piston (9) passage to return system pressure. This reduces the force acting on the control piston. Now
system pressure acting on the upper piston (7) is greater than the return system pressure on the control piston. The
result is that the upper piston in the rotating cylinder block moves the wobbler plate (8) toward the right, thus reducing the
angle of the wobbler plate. The reduced angle reduces the torque output and consequently the speed of the motor.
4-119
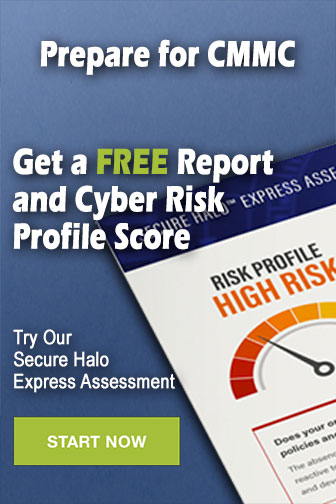