TM 1-1500-204-23-2
a. Flareless Fittings. The main feature of MS
fittings is that they can be used to connect unflared
tubing. An MS fitting has a counterbore in which the
tube end is Installed. In the half-sectional view of an
MS fitting in figure 4-17, notice the 24-degree beveled
portion of the counterbore and its seat. The seat forms
a slope for the tube during the connection of one tube
to another tube or for a tube to a component and the
beveled area causes the tube connector sleeve to seal
the connection as the tube B-nut is tightened.
(1) Identification of flareless fittings. MS fit-
tings are made of aluminum alloy or steel Aluminum
alloy fittings can be identified visually by their yellow
color, which is caused from the anodizing treatment.
The cadmium plating on steel fittings are identified by
letter-number codes; for example, MS21900-4, which
is interpreted as follows:
MS........prefix (military specification)
21900...design part number (adapter, flare-
less tube to AN flared tube)
4..........size of fitting in sixteenths of an inch (4/16 (inch)
The material from which the fittings are made is indi-
cated by the absence of a letter at the end of the MS
number or by the addition of a letter at the end of the
number, for example:
MS21900-4 is made from carbon steel
MS21900-8-D is made from aluminum
alloy
MS21900-8-S is made from corrosion-
resistant steel, class 347
(2) Types of flareless fittings. See figure 4-18
for examples of MS flareless fittings.
WARNING
Compressed air shall not be used for cleaning pur-
poses unless reduced to less than 30 psi and then
only with effective chip-guarding and personal
protective equipment.
(3) Installation of flareless fittings. MS fittings
must be inspected before Installation. If It Is Impossible
to see through a fitting or tube, blow clean, dry com-
pressed air through it to be certain that no obstructions
exist. Any lines that have caps removed in storage or
before installation should be flushed with clean
hydraulic fluid. Male threads and sleeves of the fittings
being assembled should be lubricated with the type of
hydraulic fluid used in the system On fittings with
tapered threads, use antiseize compound on the
threads, except for the first three, which are left dry.
(a) Gasket. To make a connection be-
tween tubing and a component, the proper gasket is
selected, lubricated, and Installed In position as shown
in figure 4-19. The fitting is screwed into the boss of the
component until it bottoms on the boss.
(b) Installing tubing. When connecting
tubing to an MS fitting, the tube should be aligned with
the fitting and the nut should be started by hand without
excessive strain on the line (see figure 4-20). Do not
use force to align tubing Tube alignment can often be
obtained by loosening clamps on connecting lines or
by rotating fittings. Both ends of the tubing should be
connected and tightened until a decided increase In
resistance to turning of the B-nut is encountered. At
this point, tighten the clamps, ensuring that they do not
pull the tubing out of alignment and place it in a binding
position. Complete the installation by turning the B-nut
one-sixth of a turn. See figure 4-21 for turns and torque
values. Pressurize the hydraulic system and Inspect for
leaks. If leakage is noted, release system pressure and
completely loosen the B-nut. If possible, rotate the
sleeve to a new position and then retorque the B-nut
to its previous position plus one-sixth of a turn. Normal-
ly this will stop the leak, but If it does not, replace the
assembly.
4-15
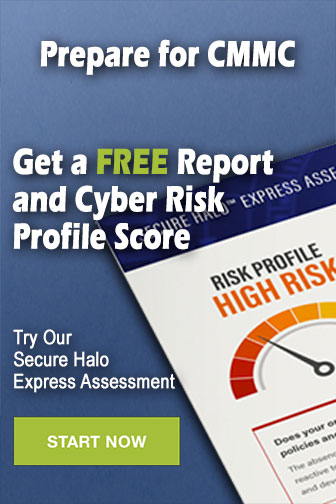