TM 1-1500-204-23-2
4 Use of table. For example, the mini-
mum standard wall thickness must be determined for a
1/2 Inch outside diameter (OD), 1/4 hard corrosion-
resistant steel tube for a 3,000 psi system. From the
above paragraph, the conversion factor is 1000. From
table 4-1 1, the nearest value must be found that applies
to this material This value is 1,120. This indicates a 1/2
inch OD x 0.028 inch tube, which is a standard size
indicated by the code d for 1/4 hard corrosion-resistant
steel.
5 Burst pressure. Taking any value from
the table, it is easy to determine the actual burst pres-
sure for a tube The following factors are multiplied by
the pressure values shown In table 4-11 to produce the
actual burst pressure
MATERIAL
BURST PRESSURE
CODE
FACTOR
a
2.9
b
6.4
c
7.5
d
1.2
For example, the system pressure producing 10,000 psi
stress on the wall of a 1/4 Inch OD x 0.012 annealed
corrosion-resistant steel tube is 960 If the system pres-
sure is 1,500 psi, the minimum burst pressure is 6,000.
Multiplying 960 by the burst pressure factor of 7.5 for
this material, the actual burst pressure is 7,100 psi, well
above the minimum of 6,000 required for this system.
(b) Layout. A piece of tubing approximately
10 percent longer than length of tubing to be replaced
should be cut. After required bends have been made,
new tubing may be 1/2 to 2 inches longer than old
tubing Allowances should be made for flaring opera-
tin. The amount of tubing in excess of amount required
to flare tube should be cut off.
NOTE
After cutting, bending, and flaring opera-
tins, oxygen tubing assemblies should be
cleaned in accordance with paragraph 4-2g
(2)
d. Template. A path should not be selected that
requires no bends unless original tubing had a path with
no bends A section of tubing cannot be cut and flared
accurately enough to be Installed without bends and still
avoid initial mechanical strain on tubing except In
straight runs not having rigid connections on each end.
A fluid line is a mechanical part when installed, and Is
sensitive to vibration; therefore, direct, straight-line con-
nektons shall never be made between two solid fixed
attachment points, as bends allow tubing to expand and
contract under temperature differences. All bends shall
be started a reasonable distance from fittings, so sleeve
and nut can be slipped back along tubing for inspection.
This will also prevent tubing from binding against
sleeve Tubing assemblies shall be formed prior to in-
stallation so it will not be necessary to pull assembly into
alignment by use of coupling nut If old tubing is intact
and the bends have not been changed, It may be used
as a template. If rerouting is required and a new
template must be made, proceed as follows:
1 Place material selected for use as a template
into one of the fittings where tube is to be connected.
2 Form necessary bends In template.
3 Remove template and use pattern to
bend new tube
4 Select path with least total degrees
bend. This reduces flow loss and simplifies bending.
5 Use path, if possible, with all bends In
same plane.
6 Lay out path which provides for either
brackets or clamps to be used as supports at intervals
not greater than those given In table 4-12.
4-5. Flexible Hose Assemblies. Flexible hose is
used In aircraft plumbing to connect moving parts with
stationary parts in locations subject to vibration or where
a great amount of flexibility is needed. It can also serve
as a connector In metal tubing systems
WARNING
Do not use flexible hose and hose as-
semblies in oxygen systems, as they readily
absorb grease and oil. Failure to comply may
result in damage to aircraft of Injury to per-
sonnel
a. Identification of Flexible Hose. Aircraft hose or
hose assemblies can be readily identified as to age and
4-32
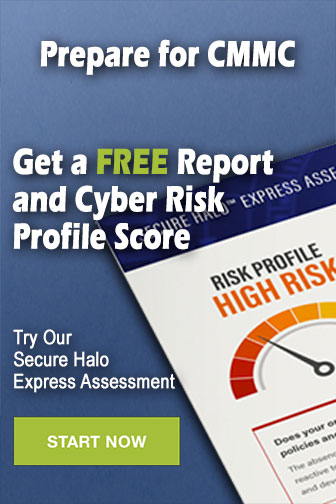